WHAT IS SIX SIGMA?
Before you begin getting into the details of Six Sigma one of the first word of advice for any six sigma novice by Six Sigma Master Black Belt John Vandenbemden –
“Don’t bite off more than you can chew, and really understand the methodology before attempting large Six Sigma projects.”
About Six Sigma
You may see people around you wanting to learn six sigma just because it is trending. Well this is not a sufficient reason enough to follow some technology. You have to have a good hand holding about its evolution and present functionalities.
There is in fact a pretty long story behind the emergence of Six Sigma, but before you really begin getting it into the details of Six Sigma, let us understand formally what is Six Sigma?
Six Sigma Definition –
“Six Sigma can be defined as a methodology that uses organizational tools with an objective to improve the capability of their business processes.”
The ultimate objective of implementing Six Sigma is to –
- Increase performance
- Decrease process variation
- Reduced defects
- Profit enhancement
- Boosting employee morale
- Improving quality of products or services.
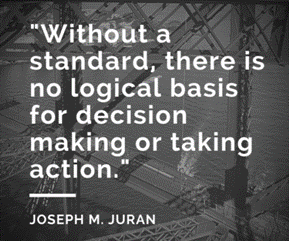
In general, the term Six Sigma quality is used to indicate whether a process is well controlled or not that is it is within process limits ±3s from the center line in a control chart, and requirements/tolerance limits ±6s from the center line. As you may see below is a standards six – sigma normal distributed curve indicating mean, standards deviation and defects to indicate the final six sigma quality of the process.
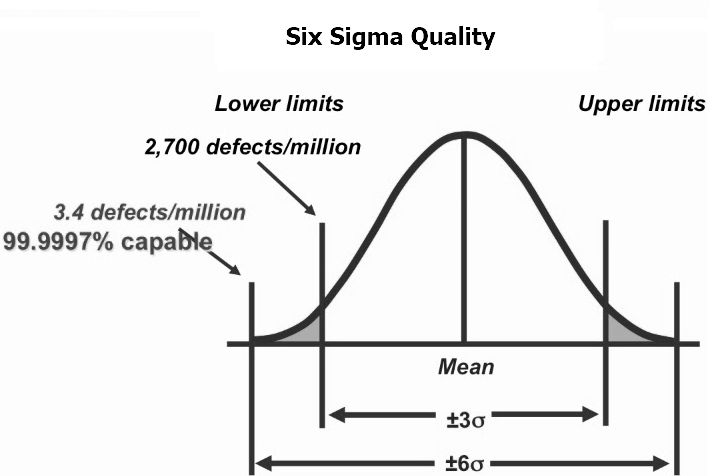
Some of the other definitions proposed for Six Sigma, with some common threads –
- “Use of teams that are assigned well-defined projects that have direct impact on the organization’s bottom line”
- “Training in ‘statistical thinking; at all levels and providing key people with extensive training in advanced statistics and project management. These key people are designated ‘Black Belts.’ Review the different Six Sigma belts, levels and roles.”
- “Emphasis on the DMAIC approach to problem solving: define, measure, analyze, improve, and control.”
- “A management environment that supports these initiatives as a business strategy.”
In layman terms, we may say that six – sigma is primarily an approach to data-driven management that seeks to improve quality by measuring the number of defects within the process and systematically eliminating them until there are as close to zero defects as possible.
To give you an overview of six sigma, in 1984 Bill Smith a Motorola engineer developed the Six Sigma management system with an objective to reduce variations in Motorola’s electronic manufacturing processes causing product defects. Ever since then these strategies, tools and cultural norms that support the management system are adopted by organizations and across industries such that the meaning of the word ‘defect’ has been extended to take consider any deficiency that hinders a company from meeting its customer’s needs.
The Greek letter sigma () is used to denote standard deviation from the mean.
During 1920s, Walter Shewhart pioneer of statistical quality control anticipated that in the process of manufacturing three sigma from the mean is considered as the point indicating a lot of defects in the process and requires rectification. These norms were accepted for many years, until Bill Smith planned to gather and analyze data at a more refined level thus making six sigma the point at which a process has to be rectified. Also it is impossible to achieve zero defects referred as ‘infinity sigma’ such that six sigma allows for 3.4 defects per million opportunities for a defect to occur in contrast to three sigma that allows for 66,807 defects per million opportunities.
Companies using six – sigma after collecting the necessary data use statistics to create a baseline sigma. This baseline elaborates as to how close or far – the company is from achieving six sigma level and thereby serve as a measuring stick for assessing future improvement. The supporters of Six Sigma claims that its benefits include up to 50% process cost reduction, cycle-time improvement, reduced wastage of materials, leading to better understanding of customer requirements, increased customer satisfaction, and more reliable products and services.
Motorola hold the federal trademark for Six Sigma and generally acknowledges that Six Sigma can be costly to implement and can take several years before a company begins to see bottom-line results. During 1995, General Electric CEO Jack Welch’s every public endorsement of Six Sigma helped businesses outside of manufacturing to assist in understanding how Six Sigma methodologies can be implemented to improve customer satisfaction in a given industry.
History of Six Sigma
You may be want to just hop over to the next section because who wants to know the history of something, we live in present and want to know how to improve our present.
Agreed!
But if our practitioners and researchers would have thought the same then probably there would have been no evolution. As a rule of thumb if you want to improve your present you must learn from your past so as to avoid the same mistakes and move towards better innovation.
We in today’s time are probably very familiar with the concept of continuous improvement – that involves the consistent and ongoing effort to improve processes, products, or services. Therefore as a professional in Six Sigma, it will be your responsibility of showing your organization the way to improve quality and thereby decreasing costs.
We shall now discuss the groundwork and a brief history of various approaches that eventually led to the evolution of Six Sigma.
With the Industrial Revolution and the advent of advanced machines the early concept of quality changed, which was previously considered hit or miss and largely determined by the skills of individual craftsmen. Ever since the 1900s, continual innovations in the means of production, tools and machines led to an explosive growth in the production of goods that has continued to this day. In addition to this innovation in the means of production led to the evolution in the tools, methods, techniques, and approaches used for quality control and continuous process improvement.
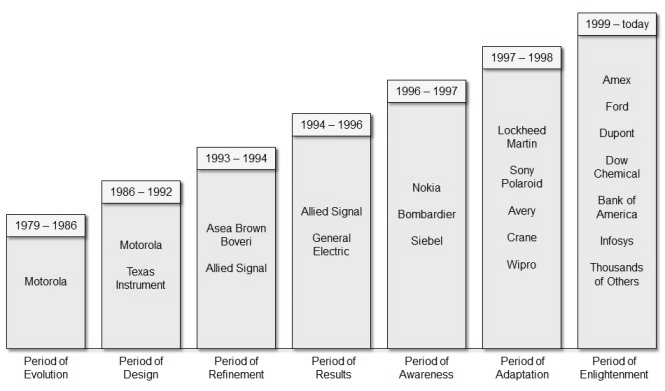
Some of the crucial events, approaches, methods, and tools considered important in the history of continuous process improvement include –
- Plan-Do-Check-Act (PDCA) cycle
- Statistical Process Control (SPC)
- Quality Circles
- Total Quality Management (TQM) And ISO 9000
- Baldrige Criteria For Performance Excellence
In the 1920s the two most important methods were developed namely –
- PDCA Cycle: PDCA cyclewas developed by W.S. Shewhart in the 1920s which was later improved by Deming. PDCA is an iterative problem-solving loop that is the basis for nearly all continuous process improvement approaches, especially in Lean manufacturing
- Control Charts: Also referred as Shewhart control charts were invented to control process variation. In the later stages, control charts became the basis of statistical process control (SPC),an important element in continuous process.
Seven pioneers of the quality sciences
- Walter Shewhart
- W. Edwards Deming
- Joseph Juran
- Kaoru Ishikawa
- Genichi Taguchi
- Armand Feigenbaum
- Philip Crosby
Quality sciences received a boost during the Second World War when the U.S. Army adopted control charts and statistical techniques to assist in the manufacture of arms, equipment, ships, planes, and other warfare needs. After the war, the quality of U.S. products fell by the edge as American companies abandoned quality in their pursuit for higher profits. During the same time quality movement traveled to Japan where Dr. Deming and Dr. Juran, among others, went to Japan after the war to help the Japanese people stimulate the economy.
In this process, engineers at Toyota adapted what they learned, by building a comprehensive methodology known as the Toyota Production System. Toyota Production System became a forerunner of Lean manufacturing, with the system focused on eliminating waste, reducing inventory, and speeding up processing time. Additionally, Toyota engineers learned how to tap into the power of their workforce for continuous process improvement. For this they invented quality circles in which case independent teams of six to eight employees meet periodically to identify opportunities for improvement and submit them to management.
By the 1980s, using the new manufacturing methodology, Japanese industries demolished what were considered to be traditionally American markets. U.S. industries struggled to find ways to meet the challenge. Some of the continuous improvement methodologies that led to prominence during this time were-
- Total Quality Management: Also referred as TQMwas invented in Japan in the 1950s. However, it achieved the status in the 1980s. TQM is a comprehensive set of management practices and tools with the primary focus on meeting or exceeding customer requirements. The emphasis of TQM is on process measurement and controls that seek to involve all employees in process improvement.
- ISO 9000: ISO 9000is a set of standards that helps businesses to organize for producing high-quality goods. Every company certified as ISO 9000 is required to conduct their business locally and internationally with an assurance of an agreed-upon quality standards.
The objective of both TQM and ISO 9000 was to help the organization “trim the fat” and improve quality. However, there were still many companies that were not interested to spend time and money on quality.
This led to potentially disastrous consequences, which then required the establishment of the Malcolm Baldrige National Quality Award in an attempt to inspire companies to achieve higher quality. The Malcolm Baldrige National Quality Award is given annually to companies that exemplify innovation, excellence, and world-class performance. The Baldrige Criteria for Performance Excellence are published by the National Institute of Standards (NIST) to provide guidance for companies that seek to establish excellence in performance management. Indeed evolution is messy and ideas appear long before they are actually implemented, therefore at times it becomes difficult to pinpoint when events occurred. Yet while describing the evolution of Lean and Six Sigma, it becomes important to understand the order in which continuous improvement approaches gained prominence in the quality sciences. Late 1980’s and early 1990’s marked the beginning of improvement in quality sciences. Some of the additional methods that emerged during this time are –
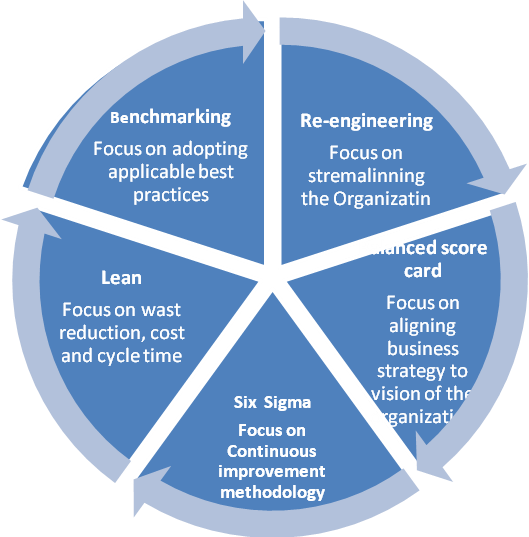
- Benchmarking: Benchmarkingis defined as a strategy for improving the organization by adopting applicable best practices of industry leaders. It helps an organization to identify what it does well and not so well, and thereby follow and adapt the leaders’ processes in order to achieve superior performance levels. Certainly benchmarking did not influence the evolution of Six Sigma directly but, it became a widely accepted method in Six Sigma for setting improvement goals and for identifying best practices and improvement solutions in order to deliver superior performance with high quality products and processes.
- Re-engineering: Re-engineeringis defined as a methodology for streamlining the organization. Many companies by the 1990s had built according to the traditional pyramid with top-heavy turf-guarding, empire-building executives. But the rigid divisional boundaries protected the status quo and prevented innovation. In 1993 Michael Hammer and James Champy urged senior management to throw everything out and build back with less staff and on the basis of processes rather than along functional lines. This re-engineering movement went successfully and thereby streamlined many organizations with their functions and objectives.
- Balanced scorecard: Balanced score card is referred as a method of aligning business activities to the vision and strategy of the organization. The methodology aims to improve internal and external communications together with monitoring the organizational performance against strategic goals. Balanced scorecard evolved in France and at General Electric in the 1950s, but it was popularized by Robert S. Kaplan and David P. Norton.
- Six Sigma: The era of early and mid-1980s faced bitter competition from Japan. Motorola created a new quality initiative from elements in the mainstream quality control movement. Motorola named its invention as ‘Six Sigma’. Six Sigma was popularized by Jack Welch at General Electric in the mid-1990s, at present it is one of the world’s most popular continuous improvement methodologies. The main objective of Six Sigma is continuous improvement by using techniques and a specialized toolkit to drive products and services to near perfection by reducing variation and defects through the application of sophisticated statistical techniques.
- Lean: The development of Toyota Production System in Japan in the 1950s and 1960s continued to fascinate quality engineers into the 1990s. By 2000, many organizations had sufficient experience with the methods and tools to successfully implement the methodology, now renamed Lean. The primary focus on Lean is to manufacture without waste. Lean tools are used to reduce waste, cost, and cycle time, and improve process flow. Lean is also being used successfully in non-manufacturing concerns.
The primary focus on quality improvement intensified during the late 1980s and 1990s, reaching an evolutionary apex with Six Sigma and Lean.
Characteristics of Six Sigma
You are aware about the methodology that is currently at the peak of the continuous improvement evolution – ‘Six Sigma’.
Six Sigma evolved directly from mainstream quality control methods. During the 1970s, a Japanese company took over a Motorola plant that produced TV sets. Thereafter the Japanese corporate leaders changed the management and workflow, and retained the workforce, technology, and designs. The factory was soon producing TV sets with approximately 1/20 of the number of defects. Motorola then realized that in order to survive, it had to change according to changing trends.
During the mid-1980s, Motorola CEO Bob Galvin launched the Six Sigma methodology, which turned the company around. Due to this implementation of Six Sigma, Motorola was able to save $16 billion and win the Malcolm Baldrige National Quality Award in 1988. In 1995, Jack Welch converted General Electric into a Six Sigma operation with legendary results. After which, the popularity of Six Sigma really took off. Six Sigma integrates the work of many quality pioneers, as well as proven approaches and techniques that came before.
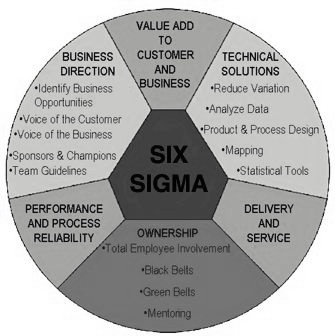
What are the six sigma characteristics?
- Emphasis on the DMAIC approach to solve problems
- DMAIC is based on the PDCA improvement cycle.
- Requires rigorous application of statistics
- Uses statistical tools in all phases of DMAIC, particularly in the Analyze, Improve, and Control phases.
- Uses proven tools and techniques for defect reduction
- Process and quality-related issues are addressed by using Six Sigma statistical, strategic, financial, analytical, project management, and business tools.
- Uses well-trained, independent teams to handle well-defined projects
- Uses independent teams and worker participation pioneered by the Japanese with quality circles and the gemba methodology.
- Requires reorganization to focus on processes and quality, rather than functional domains
- Re-engineering, TQM, and ISO 9000 all advocate a process-oriented approach to organizing for quality.
Goals of Six Sigma
We need to clearly understand what is the main goal of a six sigma implementation?
Aligning ‘voice of the process’ with the ‘voice of the customer’ – Voice of the process describes the amount of variation in a process, measured on a bell curve where on the other hand voice of the customer describes what the customer expects from a product or customer specification.
There are majorly two main goals of Six Sigma, we shall now understand the various goals for implementing six sigma –
- Reducing variation and achieving high quality: You will agree that there is always some amount of variation in any given process, but when the process variation goes outside the customer specification limits then it becomes unacceptable to the customer. Six Sigma seeks to identify causes of unacceptable variation and eliminate them, thereby achieving a consistently high level of quality in products and services.
- Reducing defects to achieve six sigma levels: In ideal situation, companies operating at six sigma level deliver products or services that are 99.9997% defect free that corresponds to 3.4 defects per million opportunities. Such high six sigma standards set an extraordinarily high level of excellence.
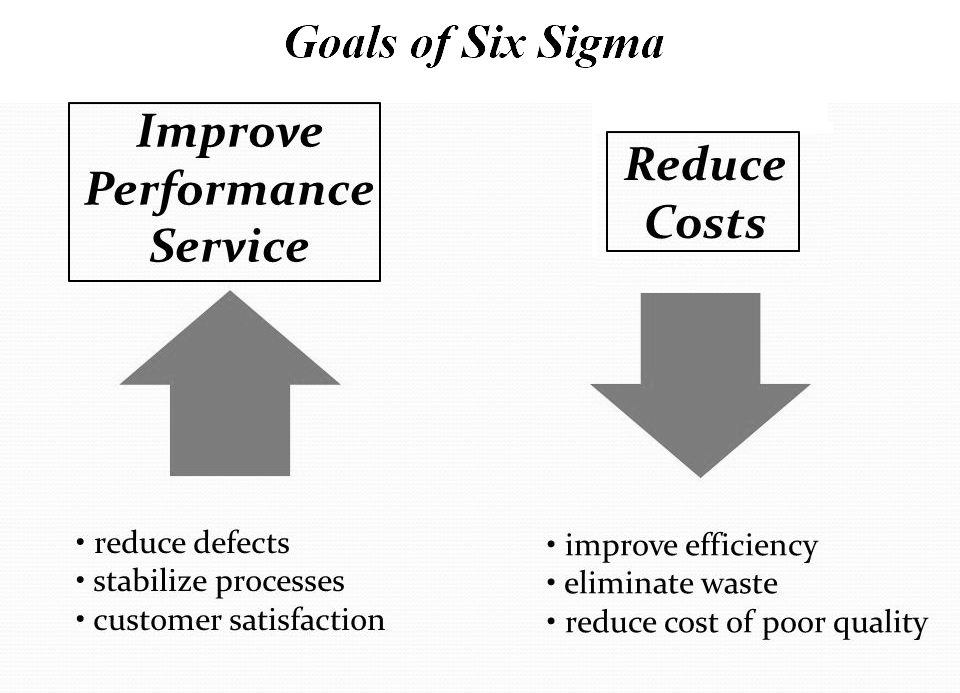
It’s time to lean and become a six sigma professional take Vskills Practice test on Six Sigma
Doctrine of Six Sigma
The doctrine of six sigma asserts the following –
- Firstly it asserts continuous efforts to achieve stable and predictable process results that are of essential for the business success (Example – By reducing process variation).
- Secondly the six sigma asserts that manufacturing and business processes posses all the characteristics that can be defined, measured, analyzed, improved, and controlled.
- Thirdly it asserts that achieving sustained quality improvement requires commitment from the entire organization, and specifically from the top management.
Some of the additional features that set Six Sigma apart from previous quality-improvement initiatives are –
- Focus on achieving measurable and quantifiable financial returns from any Six Sigma project.
- Increased emphasis on strong and passionate management leadership and support.
- Most importantly commitment to make decisions on the basis of verifiable data and statistical methods, rather than assumptions and guesswork.
The term “Six Sigma” comes from statistics and is used in statistical quality control, to evaluate process capability. Formally, it is referred to the ability of manufacturing processes to produce a very high proportion of output within specification.
Therefore any process that operates within “six sigma quality” over the short term is assumed to produce long-term defect levels below 3.4 defects per million opportunities (DPMO). Here, the 3.4 DPMO is based on a “shift” of +/- 1.5 sigma created by the psychologist Dr Mikel Harry.
Mikel Harry created this number based on the tolerance in the height of a stack of discs. Ideally, Six Sigma’s implicit goal is to improve all processes, but not to the 3.4 DPMO level necessarily. The organization is required to determine an appropriate sigma level for each of their most important processes and strive to achieve the result. This leads to incumbent on management of the organization to prioritize areas of improvement.
Six Sigma was registered on June 11, 1991 as U.S. Service Mark 1,647,704. In 2005 Motorola attributed over US$17 billion in savings to Six Sigma.
Some of the other early adopters of Six Sigma include Honeywell and GE, where Jack Welch introduced this methodology. By the end of 1990s, about two-thirds of the Fortune 500 companies started with Six Sigma initiatives with the sole objective of reducing costs and improving quality.
In earlier years, practitioners have also combined Six Sigma ideas with lean manufacturing to create a methodology named Lean Six Sigma. Primarily, the Lean Six Sigma methodology considers lean manufacturing to tackle process flow and waste issues, together with Six Sigma, having focus on variation and design, since corresponding disciplines aim at promote business and operational excellence.
Various companies like GE, Accenture, GENPACT, and IBM use Lean Six Sigma techniques to focus on transformation efforts and not just on efficiency but with emphasis on growth. The technique serves as a foundation for innovation throughout the organization from manufacturing and software development to sales and service delivery functions.
Six Sigma Methodologies
Primarily the projects using Six Sigma methodology follow two project methodologies inspired by Deming’s Plan-Do-Study-Act Cycle. These methodologies, composed of five phases – DMAIC and DMADV.
- DMAIC Methodology is used for projects aimed at improving an existing business process.
- DMADV Methodology is used for projects aimed at creating new product or process designs.
DMAIC
DMAIC is considered as a data-driven quality strategy used by organizations to improve processes. DMAIC is considered as an integral part of a Six Sigma initiative, but usually this methodology can be used to implement as a standalone quality improvement procedure or as part of other process improvement initiatives like lean.
DMAIC process is the key technique that lends itself to the project approach to quality improvement encouraged promoted by Juran.
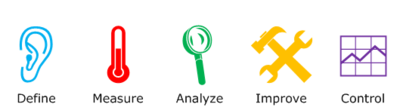
Phases of DMAIC
Five phases of DMAIC project methodology are –
- Define Phase – This phase involves defining the system, the voice of the customer and their requirements, and the project goals, explicitly.
- Measure Phase – The measure phases involve measuring key aspects of the current process and collect relevant data and calculate the Process Capability.
- Analyze Phase – In this phase data analysis is done to investigate and verify cause-and-effect relationships in order determine the relationships, and attempt to ensure that all factors have been considered. Thereby seek out root cause of the defect under investigation.
- Improve Phase – In this phase the objective is to improve or optimize the current process based upon data using various techniques such as design of experiments, poka yoke or mistake proofing, and standard work to create a new, future state process. Thereby setting up pilot runs to establish process capability.
- Control Phase – In the fourth phase the objective is to control the future state process so as to ensure that any deviation from the target is rectified before resulting into defects. This phase involves implementing control systems such as statistical process control, production boards, visual workplaces, and continuously monitor the process. The process needs to be repeated until the desired quality level is attained.
Let us consider a flow chart that will give you a better understanding of the process
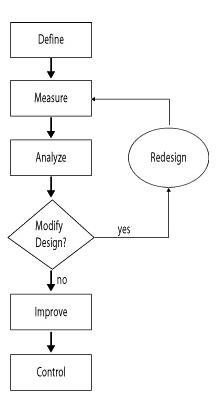
There are some organizations add a recognize step at the beginning, which is to recognize the right problem to work on, thereby leading to an RDMAIC methodology.
In layman terms DMADV is a project methodology also referred as DFSS (Design For Six Sigma), that features five phases of implementation.
DMADV is a Six Sigma framework with focus on the development of a new service, product or process in contrast to improving a previously existing one. This approach – Define, Measure, Analyze, Design, Verify is primarily helpful during the implementation of the new strategies and initiatives due to its basis in data, early identification of success and detailed analysis.
More important is to understand when to apply DMADV methodology?
- While a non-existent product or process needs to be developed at a company or
- When an existing process or product already exists yet needs to meet a Six Sigma level or match the customer specification.
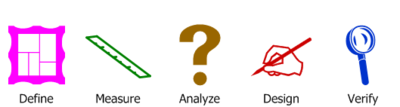
Five steps of DMADV
- Define Phase – In the first phase you are required to define design goals that are consistent with customer demands and the enterprise strategy.
- Measure Phase – In the next step you are required to measure and identify characteristics that are Critical to Quality, measure product capabilities, production process capability, and measure risks.
- Analyze Phase – In the third phase you are required to analyze to develop and design alternatives
- Design Phase – In the fourth phase you are required to design an improved alternative, best suited per analysis as per the previous step
- Verify Phase – In the last phase you are required to verify the design, perform pilot runs, implementing the production process and thereby hand over to the process owner(s)..
Tools of Quality management
With reference to the individual phases within DMAIC or DMADV project, the Six Sigma methodology uses many established quality-management tools which can also be used outside Six Sigma. The following table shows an overview of the main methods used.
- 5 Whys
- Statistical and fitting tools
- Analysis of variance
- General linear model
- ANOVA Gauge R&R
- Regression analysis
- Correlation
- Scatter diagram
- Chi-squared test
- Axiomatic design
- Business Process Mapping/Check sheet
- Cause & effects diagram (referred as fishbone or Ishikawa diagram)
- Control chart/Control plan (referred as a swimlane map)/Run charts
- Cost-benefit analysis
- CTQ tree
- Design of experiments/Stratification
- Histograms/Pareto analysis/Pareto chart
- Pick chart/Process capability/Rolled throughput yield
- Quality Function Deployment (QFD)
- Quantitative marketing research through use of Enterprise Feedback Management (EFM) systems
- Root cause analysis
- SIPOC analysis (Suppliers, Inputs, Process, Outputs, Customers)
- COPIS analysis (Customer centric version/perspective of SIPOC)
- Taguchi methods/Taguchi Loss Function
- Value stream mapping
Six Sigma Certification Belts
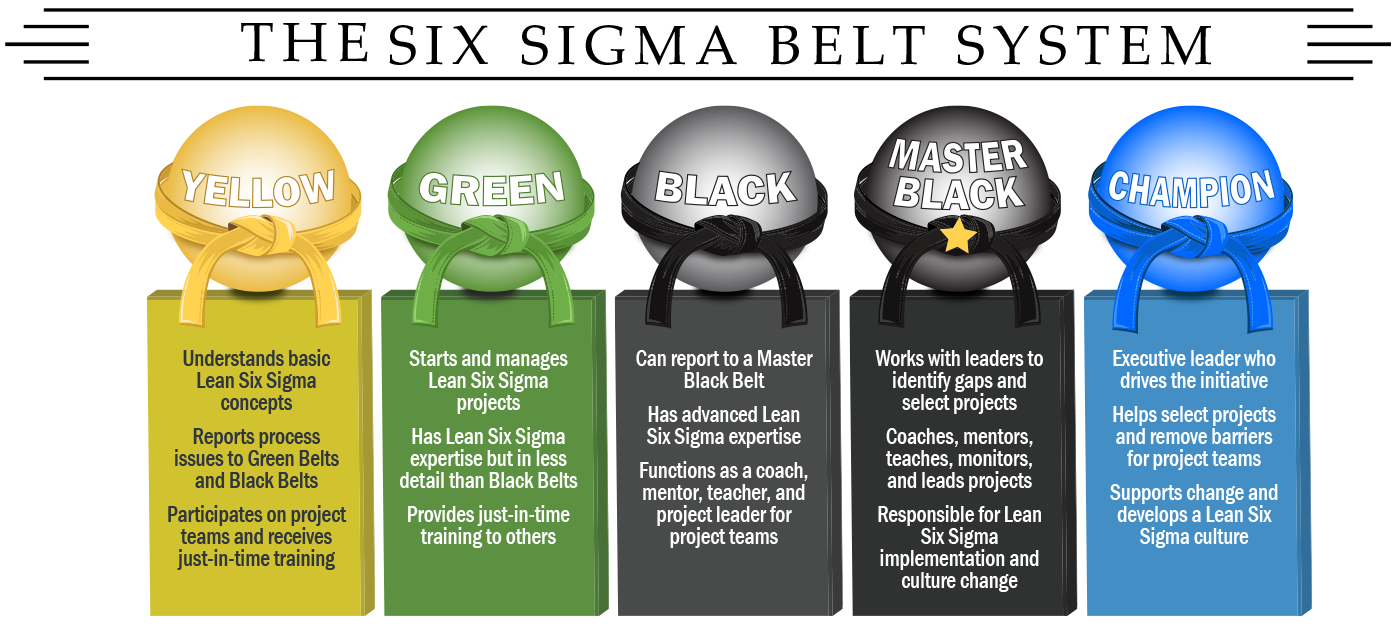
Six Sigma management consists of several levels of six sigma certification, such as – Six Sigma Yellow Belt, Six Sigma Green Belt, Six Sigma Black Belt, and Master Black Belt, Six Sigma Champion.
We will now discuss each level of certification in detail –
SIX SIGMA YELLOW BELT
A Six Sigma Yellow Belt professional is the most basic form of Six Sigma certification. Yellow Belt professionals are required to understand the theory behind Six Sigma management but do not have the quantitative skills to function as an active Six Sigma project team member.
SIX SIGMA GREEN BELT
Six Sigma Green Belt professionals are individual who are required to work part-time (25%) on projects, and also work as a team member for complex projects, or as a project leader for simpler projects. In general, Green belts are considered as the “work horses” of Six Sigma projects. One of the critical prerequisite for progression into upper management in a Six Sigma organization is to have a Green Belt certification.
Responsibilities of a Six Sigma Green Belt Professional
- Required to refine a project charter.
- Required to review the project charter with the project’s champion.
- Required to select the team members for the project.
- Required to communicate with the champion, master black belt, black belt and process owner throughout all stages of the project.
- Required to facilitate the team through all phases of the project.
- Required to schedule meetings and coordinate logistics.
- Required to analyze data through all phases of the project
- Required to train team members in the basic tools and methods of Six Sigma.
Also in complex Six Sigma projects, green belts are required to work closely with their team leader so as to maintain smooth functioning and progression through the various stages of the Six Sigma project.
SIX SIGMA BLACK BELT
Six Sigma Black Belt professionals are also referred as a full-time change agent and improvement leaders. They are required to be an expert in the process under study.
Pre-requisites for a Six Sigma Black Belt
- Posses technical and managerial process improvement and innovation skills.
- Must have a passion for Statistics and Systems Theory.
- Must understands the psychology of individuals and teams.
- Must have a good understanding of process improvement tools and methods.
- Possess excellent communication and writing skills.
- Should be able to work well in a team format.
- Excellence in manage meetings.
- Posses a pleasant personality and good team spirit.
- Focus on customer focus.
Responsibilities of Six Sigma Black Belt
- Required to prepare a project charter.
- Must communicate with the champion and process owner about progress of the project.
- Required to lead the project team.
- Required to schedule meetings and coordinate logistics.
- Must be able to assist the team members design experiments and analyze the data required for the project.
- Provide training in tools and team functions to project team members.
- Required to help team members prepare for reviews by the champion and executive committee.
- Required to lead and coach Green Belts leading projects limited in scope.
Six Sigma Black Belt is considered as a full-time quality professional mentored by a master black belt, but may also report to a manager, for their tour of duty as a black belt.
MASTER BLACK BELT
The role of a Master Black Belt is that of a leader who acts as a custodian of the Six Sigma process, and work as an advisor to executives or business unit managers, and leverages skills with the aligned projects led by black belts and green belts professionals. Often, the master black belts are required to report directly to senior executives or business unit managers. A master black belt is a confirmed change agent, leader, facilitator, and technical expert in Six Sigma project management. Master black belt is a career path where it is always suggested for an organization to grow its own master black belts. But unfortunately, at times it becomes impossible for the organization to grow its own master black belts due to the lag of time and resources to become a master black belt. Indeed it takes years of study, practice, guidance under a superior.
Responsibilities of a Six Sigma Master Black Belt
- Required to counsel senior executives and business unit managers on Six Sigma management and their processes.
- Must be able to help identify and prioritize key project areas in keeping with strategic initiatives
- Required to continually improve and innovate the organization’s Six Sigma process.
- Must be able to apply Six Sigma functionalities across both operations and transactions-based processes like Sales, HR, IT, Facility Management, Call Centers, Finance, etc.
- Required to coordinate Six Sigma projects from the dashboard.
- Must be capable to teach black belts and green belts Six Sigma theory, tools, and methods.
- Required to mentor black belt and green belt professionals.
At the executive level in Six Sigma organizations function as members of Six Sigma projects. Professionals are required to take a very active sponsorship and leadership role in conducting and implementing Six Sigma projects. Six Sigma Champion should be a member of the Executive Committee, or a trusted direct report of a member of the Executive Committee.
The champion belts should have influence to remove obstacles or provide resources without having to go higher in the organization. They work closely with the executive committee, the project leader (called a black belt) assigned to their project, and the master black belt (supervisor of black belts) overseeing their project.
Responsibilities of a Champion
- Required to identify their project on the organizational dashboard.
- Must develop and negotiate project objectives with top management.
- Must be able to select a black belt (or a green belt for a simple project) to lead the project team.
- Required to remove any political barriers or resource constraints to their Six Sigma project.
- Must be able to provide a communication link between project team(s) and top management.
- Should help team members manage their resources and stay within the budget.
- Should review each project’s timetable.
- Must be able to keep the team focused on the project by providing direction and guidance.
- Must assure that Six Sigma methods and tools are being used in the project.
Implementation roles in Six Sigma
One of major areas of innovation Six Sigma involves complete professionalization of quality management functions and processes. Before the implementation of Six Sigma, quality management practice was largely assigned to the personnel at production floor and to statisticians in a separate quality department. The official Six Sigma programs require formal ranking terminology to define a hierarchy which includes all business functions and levels as discussed in the previous sub-topic.
As we know that Six Sigma identifies several key roles for its successful implementation.
- Executive Leadership: The executive leadership includes CEO and other associate members of top management. They are primarily held responsible for setting up a vision for Six Sigma project implementation and functioning. The executive leaders empower the other six sigma members with the freedom and resources to explore new ideas for breakthrough improvements by rise above departmental barriers and overcoming natural resistance to adapt to change.
- Champions: Champions are required to take responsibility for Six Sigma project implementation across the organization in a systematically integrated manner. Under championship level, the Executive Leadership draws them from upper management. Champions are required to act as mentors to Black Belts.
- Master Black Belts: Master Black Belts are primarily identified by Champions within the team, to act as in-house coach in Six Sigma implementation. Master black belts are required to devote 100% of their time to Six Sigma. They majorly assist Champions and guide Black Belt professionals and Green Belt professionals. Besides statistical tasks, master black belt also spends their time to ensure consistent application of Six Sigma across various departments and functions.
- Black Belts: Black Belt Professionals are required to work under Master Black Belts to apply Six Sigma methodology to specific projects. Professionals are required to devote their complete valued time to Six Sigma. They mainly focus on Six Sigma project execution and special leadership with special tasks, where on the other hand Champions and Master Black Belts focus on identifying projects and the functions for Six Sigma.
- Green Belts: Green Belt Professionals are employees who are made responsible to adopt Six Sigma process implementation together with their other job responsibilities, operating under the guidance of Black Belts.
- Yellow Belts: Yellow Belts, are used for employees with basic training in Six Sigma tools and are required to participate in projects and for those locally trained in the concepts but do not participate in the project team.
According to six sigma benchmark, special training and certification is required for all of the six sigma practitioners to make sure that they follow the methodology and use the data-driven approach appropriately.
Six Sigma Process
We define six sigma process that if one has six standard deviations between the process mean and the nearest specification limit, then nearly no items will fail to meet the desired specifications. The six sigma process is based on the calculation method employed in process capability studies.
Under six sigma process the capability studies measures the number of standard deviations between the process mean and the nearest specification limit in sigma units, which is represented by the Greek letter σ (sigma). With reference to the graph as the process standard deviation increases, or the mean of the process moves away from the center of the tolerance, then fewer standard deviations will fit between the mean and the nearest specification limit, thereby decreasing the sigma number and increasing the likelihood of items outside specification.
Remember that the calculation of Sigma levels for a process data is free of the data being normally distributed. With reference to one of the disapprovals to Six Sigma, all the practitioners using this approach spend a lot of time transforming data from non-normal to normal using transformation techniques thereby leading to wastage of time. It has been said that Sigma levels can be determined for process data which has evidence of non-normality.
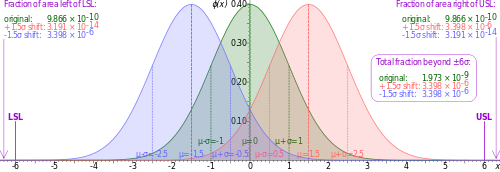
The above graph of the normal distribution indicates the statistical assumptions of the Six Sigma model. At the centre i.e., 0, the Greek letter µ (referred as mu) marks the mean, such that the horizontal axis represents distance from the mean, marked in standard deviations and given the letter σ (referred as sigma).
In which case the greater the standard deviation, the greater is the spread of values encountered. For the curve shown above, µ = 0 and σ = 1. Here the upper and lower specification limits are marked USL and LSL respectively must be plotted at a distance of 6σ from the mean. Due to the properties of the normal distribution, all the values lying that are located far away from the mean are extremely unlikely to occur approximately 1 in a billion which is too low, and the same too high.
In which case, even if the mean is made to move towards right or left by 1.5σ at some point in the future there would still be a good amount of safety cushion. This is the reason why Six Sigma aims to have processes where the mean is at least 6σ away from the nearest specification limit.
What is 1.5 sigma shift?
From experience it has been seen that has shown that processes usually do not perform well in the long term as they do in the short term. Consequently, the number of sigma units that will fit between the process mean and the nearest specification limit may as well even fall over a period of time, in comparison to an initial short-term study. In order to handle real-life increase in process variation over time, an empirically based 1.5 sigma shift is released into the calculation. In accordance with the idea, a process that fits 6 sigma between the process mean and the nearest specification limit in a short-term study will in the long term fit only 4.5 sigma either because the process mean will move over time, or because the long-term standard deviation of the process will be greater than that observed in the short term, or both cases hold.
Formally we define a six sigma process as the process that produces 3.4 defective parts per million opportunities (DPMO). This entirely is based on the fact that a process that is normally distributed will have 3.4 parts per million outside the limits, when the limits are six sigma from the original mean of zero and the process mean is then shifted by 1.5 sigma thus, the six sigma limits are no longer symmetrical about the mean. The past six sigma distribution, under the effect of the 1.5 sigma shift, is also represented to as a 4.5 sigma process. Such that the failure rate of a six sigma distribution with the mean shifted towards 1.5 sigma is not correspond to the failure rate of a 4.5 sigma process with the mean centered on zero. Therefore special causes may result in decline in process performance over time and is majorly designed to avoid underestimation of the defect levels that are likely to be encountered in real-life operation.
You must understand that the role of the sigma shift is majorly academic. The objective of six sigma is to make organizational performance improvement. Therefore it is up to the organization to determine the six sigma level, based on customer expectations. Here the purpose of the sigma value is to have a comparative figure so as to identify if a process is improving, deteriorating, stagnant or non-competitive with others in the same business. Here, six sigma i.e., 3.4 DPMO is not the sole objective of all processes.
Levels of Sigma
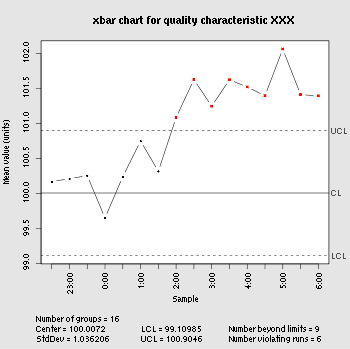
Let us consider the above control chart that represents a process that has undergone a 1.5 sigma drift in the process mean toward the upper specification limit starting at midnight. Now, the control charts are majorly used to maintain 6 sigma quality level by indicating when quality professionals should start investigating a process to find and eliminate special-cause variation.
Following table shows long-term DPMO values corresponding to various short-term sigma levels.
Sigma level | Sigma (with 1.5σ shift) | DPMO | Percent defective | Percentage yield | Short-term Cpk | Long-term Cpk |
1 | −0.5 | 691,462 | 69% | 31% | 0.33 | −0.17 |
2 | 0.5 | 308,538 | 31% | 69% | 0.67 | 0.17 |
3 | 1.5 | 66,807 | 6.7% | 93.3% | 1.00 | 0.5 |
4 | 2.5 | 6,210 | 0.62% | 99.38% | 1.33 | 0.83 |
5 | 3.5 | 233 | 0.023% | 99.977% | 1.67 | 1.17 |
6 | 4.5 | 3.4 | 0.00034% | 99.99966% | 2.00 | 1.5 |
7 | 5.5 | 0.019 | 0.0000019% | 99.9999981% | 2.33 | 1.83 |
When we analyse the table carefully it can be seen that these figures assume that the process mean will shift by 1.5 sigma towards the side with the critical specification limit. Therefore we can say that if they assume that after the preliminary study involving determination the short-term sigma level, the long-term Cpk value will turn out to be 0.5 less than the short-term Cpk value.
Lets take up an example to illustrate this further, suppose the DPMO figure given for 1 sigma assumes that the long-term process mean will be 0.5 sigma beyond the specification limit (i.e., Cpk = –0.17), rather than 1 sigma within it, as it was in the short-term study (Cpk = 0.33). Remember that the defect percentage signifies only defects exceeding the specification limit to which the process mean is nearest, such that defects beyond the far specification limit are not included in the percentages.
D P M O = 1 , 000 , 000 ⋅ ( 1 − ϕ ( l e v e l − 1.5 ) ) {\displaystyle DPMO=1,000,000\centerdot (1-\phi (level-1.5))}
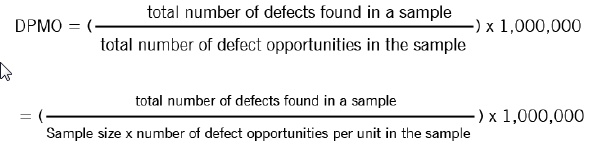
Application of Six Sigma
In general, Six Sigma mostly finds its application in large organizations. One of the most crucial factor in the spread of Six Sigma was General Electricals announcement in 1998 of saving $350 million with thanks to Six Sigma, which further grew to more than $1 billion. Six Sigma contains a large number of tools and techniques which work well in small to mid-size organizations. Even though an organization may not be big enough to be able to afford and implement all the six sigma approaches but that does not diminish its abilities to make improvements using certain set of tools and techniques. The infrastructure is depicted as necessary to support Six Sigma as a result of the size of the organization rather than a requirement of Six Sigma itself.
Even though the scope of Six Sigma may differ based on its implementation, it can still successfully deliver its benefits to different applications.
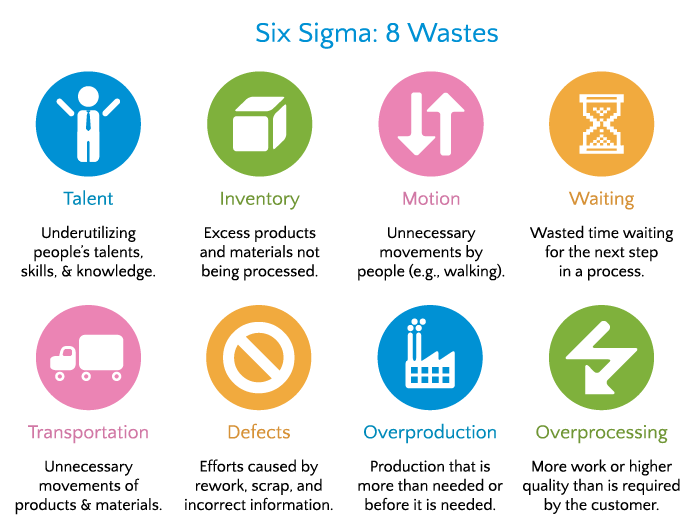
In the late 1980s, after its first application at Motorola, there were other internationally recognized firms who recorded high number of savings after applying Six Sigma. Some of the common examples are – Johnson and Johnson ($600 million savings), Texas Instruments($500 million savings) as well as Telefónica de Espana ($30 million Euros of revenue in the first 10 months). Also there were other organizations like Sony and Boeing who were able to achieve large percentages in waste reduction.
We have seen companies implementing common quality control and process improvement strategies, yet there is still need for more reasonable and efficient methods as desired standards and satisfaction of the client have not always been reached. There is still a need for necessary analysis to control the factors affecting concrete cracks and slippage between concrete and steel (let us suppose). With reference to a case study on Tinjin Xianyi Construction Technology Co, Ltd., it was seen that construction time reduced by 26.2% and construction waste declined by 67% after implementing Six Sigma techniques. Another case study of study was considered at one of the largest engineering and construction companies in the world – ‘Bechtel Corporation’ such that it was seen that after an initial investment of $30 million in a Six Sigma program (involved identifying and preventing rework and defects) over $200 million were saved.
The implementation of Six Sigma played a crucial role in improving the accuracy of allocation of funds to reduce bank charges, foster automatic payments, improving accuracy of reporting, reducing documentary credits defects, minimizing check collection defects, and reducing variation in collector performance. The financial institutions who reported considerable improvements in their operations are – Bank of America and American Express.
It was observed that Bank of America were able to increase the customer satisfaction by 10.4% thereby decreasing customer issues by 24% with the application of Six Sigma tools in their streamline operations. Likewise, American Express were able to successfully eliminate non-received renewal credit cards and improved their overall processes with the help of Six Sigma principles. The six sigma strategy is also applied by other financial institutions like GE Capital Corp., JP Morgan Chase, and SunTrust Bank, with the solve objective of customer satisfaction.
In the field of supply chain management it becomes very important to ensure that products are delivered to clients at the right time and at the right place while preserving the high-quality standards from start till the end of the supply chain. It has been observed that six Sigma can ensure quality control on products (defect free) and guarantee delivery deadlines by changing the schematic diagram for the supply chain.
Healthcare
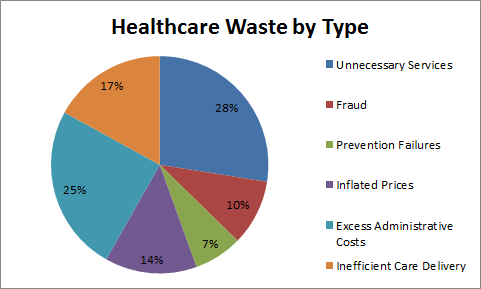
Health care is the sector that has been popularly matched with the doctrine of six sigma for many years due to the nature of the healthcare sector of zero tolerance for mistakes and potential for reducing medical errors. The primary objective of Six Sigma in the healthcare sector is very broad which includes reducing the inventory of equipment that brings extra costs, altering the process of healthcare delivery in order to make more efficient and refining reimbursements.
Six Sigma Criticism
- No uniqueness: Joseph M. Juran one of eminent quality expert described Six Sigma as a basic version of quality improvement stating that there is nothing new to it. As per him six sigma includes what we refer to call facilitators with adoption of more flamboyant terms, like belts with different colors. I think that concept has merit to set apart, to create specialists who can be very helpful.
- Insufficient for complex manufacturing: Also quality expert Philip B. Crosby stated that the Six Sigma standard does not go far enough ad the customers deserve defect-free products every time.
- Over-reliance on statistical tools: One of the direct criticisms is the firm nature of Six Sigma and its over-reliance on methods and tools. In the process of six sigma implementation more attention is paid to reducing variation and looking for significant factors where on the other hand less attention is paid on developing robustness in the first place that can be used to completely eliminate the need for reducing variation. Critics state that extensive reliance on significance testing and use of multiple regression techniques increase the risk of making unknown types of statistical errors or mistakes.
Six Sigma Professional Bodies
American Society for Quality (ASQ)
ASQ (American Society for Quality) is a global community of people dedicated to quality who share the ideas and tools that make our world work better. With individual and organizational members around the world, ASQ has the reputation and reach to bring together the diverse quality champions who are transforming the world’s corporations, organizations and communities to meet tomorrow’s critical challenges. ASQ India opened in 2010 in New Delhi, India. It brings together all of ASQ’s programs including training, certification, membership (establishing Local Member Communities) and facilitation of improvement initiatives.
Institute of Industrial and Systems Engineers (IISE)
Industrial and systems engineers make things better in any industry — from automobile manufacturing and aerospace, to healthcare, forestry, finance, leisure, and education. The Institute of Industrial and Systems Engineers, founded in 1948, helps its members improve complex organizations around the world and across industries. Throughout their careers, members turn to IISE for tools and connections that provide an integrated and systemic perspective to business challenges. Solving complex problems is our common objective.
IISE, the world’s largest professional society dedicated solely to the support of the profession, is an international, nonprofit association that provides leadership for the application, education, training, research, and development of industrial and systems engineering
Chartered Quality Institute (CQI)
The CQI is the chartered body for quality professionals with an aim to improve the performance of organisations by developing their capability in quality management. With members all over the world, CQI is uniquely placed to define and lead the quality profession, setting the standards for its capability and scope through the CQI Competency Framework. We encompass the whole quality community, including quality management professionals (CQI members) and management systems auditors, through our specialist division IRCA (the International Register of Certificated Auditors).
Vskills – India Largest Government Certification
Vskills is a certification programme run by a Government of India PSU, and a Joint Venture of TCIL ( Govt of India PSU) and DSIIDC ( A Govt of NCT Delhi PSU). Vskills is the largest certification body of India. It conducts skills testing and certification exam to improve employability. Candidates use Vskills Certifications, which are well recognized in the Industry, as certification of skills and knowledge.
Companies have benefitted by hiring pre certified candidates from Vskills and also use the certifications for their in house employee appraisals. Vskills certifications are for relevant qualifications that help students/employees quantify and prove those skills that are valued by the employer and are in great demand.
Six Sigma Software Packages
In general there are four classes of software used to support the Six Sigma process improvement namely,
- Analysis Tools – Analysis tools are used to perform statistical or process analysis
- Program Management Tools – These tools are used to manage and track a corporation’s entire Six Sigma program
- DMAIC and Lean online project collaboration tools – These tools are used for local and global teams
- Data Collection tools – These tools are used to feed information directly into the analysis tools and significantly reduce the time spent gathering data.
Some of the commonly used tools
- ARIS Six Sigma
- IBM WebSphere Business Modeler
- JMP
- Oracle Crystal Ball (part of Oracle Fusion Middleware)
- Microsoft Visio
- Minitab
- NCSS Statistical Software
- QPR ProcessGuide by QPR Software
- Quality Companion by Minitab
- RCASE
- R language (open source)
- SDI Tools
- SigmaXL
- Software AG webMethods BPM Suite
- SPC XL
- Statgraphics
- STATISTICA
- Telelogic System Architect
Pros and Cons of Six Sigma
Initially there was a lot of opposition and doubts to the six sigma methodology cropped up, with most organizations and managers avoiding it away due to its perceived statistical complexity. But over a period of time, the perception has changed as businesses increasingly adapted, tested, and altered their overall methodology for improving their operations. Many organizations have tested through implementation, and conducted study to establish underlying factors that affect an organization’s adoption of Sigma, and long-term success.
As per survey conducted on a sample, 64% of the organizations had overwhelmingly increased their profits by more than 100%, while 64% of the organizations comparatively low profits. Interestingly, 81% of the companies that were yet to successfully implement Six Sigma had registered significantly higher profits before adopting the strategy.
Pros of Six Sigma
- Ensured accomplishment: Organizations used Six Sigma methodology successfully in one or more operational and business spheres have gained immensely. We have seen Six Sigma methodology used across domains for increasing sales, stock value, customer satisfaction. One of the prime examples is GE or General Electric was able to save more than $ 8 billion in the initial 3 years of Six Sigma methodology implementation.
- Value Enhancement: Indeed Six Sigma has proved to be beneficial towards adding more value and providing improved quality to the organization’s output in the form of a product or service. As we see across, Six Sigma is used to optimize supply chain processes as well and to increase customer satisfaction. As a methodology, Six Sigma once adopted and implemented, becomes a part of business culture, such that all processes can be optimized and improved one-by-one.
- Reduced wastage and increased learning: Six Sigma methodologies help in identifying the errors and variances beforehand thereby avoiding wastage. Together with lower costs related to operations hence greater profits. Six Sigma also helps in creating a learning platform within an organization. Process documentation and analysis helps in identifying errors and variances for better insight into the business processes and their efficiency.
Cons of Six Sigma
- Complex implementation: As discussed earlier Six Sigma requires complete participation of all the employees working in the operations and other business processes making the coordination all the more difficult. It is observed that it may be easily implemented in a SME, but in particular it becomes difficult to implement Six Sigma in the large-sized business organizations.
- Complications: Since the Six Sigma methodology examines the business processes carefully with large amounts of statistical and empirical data required to be generated during its implementation. Due to which the data is required to be carefully scrutinized and analysed to find out the variances. Now this process can be very complex and complicated requiring a lot of time while performing a test run and thereby sustaining it.
- Costly in long-run: It has been observed that Six Sigma may provide for cost saving in the long run, but being a quality improvement process it is a core, therefore its repetition beyond a certain point may boost overhead and operational costs.
The Six Sigma course and certification has various skill levels including Yellow/Green/Black/Master Black Belt. Six Sigma certification holders are in high demand today. Six Sigma certified professionals provide business more competition and increase customer retention through implementing strategies that provide enhanced customer satisfaction. Six Sigma experts are valuable towards implementation of the strategic decisions, strategies, and policies and can make a number of business processes smoother and lesser time consuming while preventing wastage and errors. Management and engineering personnel (among other professionals) can obtain Six Sigma certification now to get a promotion, salary hike, better recognition and placement in the premium and Fortune 500 companies.
Future of Six Sigma
Over a period of time, Six Sigma has evolved and established itself as an effective quality improvement technique after its successful implementation in various organizations all over the world. It has been seen that various large organizations have improved the quality of manufactured goods or services delivered.
Nevertheless, the potential of Six Sigma has not been realized so far and the extent of profitability of Six Sigma in various different sectors is yet to be discovered. One of the prime reason is due to numerous competent whether small to medium level enterprises that are yet to implemented Six Sigma programs.
What could be the reason you think for not implementing six sigma?
One of the reason behind not implementing six sigma may be that these enterprises have all the resources for the implementation of Six Sigma initiatives, yet they are wary of the certification, since they believe that Six Sigma is beneficial only for large organizations.
No matter how much criticism follows, no matter what is presumed.
The future for Six Sigma programs is extremely bright and there is continuously increasing awareness in small and medium enterprises regarding the potential benefits of implementing the Six Sigma initiatives.
Indeed Six Sigma is different from other quality management tools such as TQM or Kaizen although it may appear similar. The process of implementation of other quality management programs lead to a stage where no further quality improvements can be achieved where on the other hand the focus of Six Sigma is to improve quality processes to the next level.
Six Sigma can be applied to every business process of an organization. This clearly suggests that scope of Six Sigma is much broader than other quality management programs and it may outlast them in the future.
The coming future is likely to see Six Sigma as one of the key quality techniques for improvement of management process. Since Six Sigma professionals are at all point of time making an effort to integrate Six Sigma with other existing innovative management practices to make Six Sigma method even more effective and result-oriented.
In the current scenario one of the key area of interest for researchers and practitioners in order to maximize the positive effect of the Six Sigma method involves integrating Six Sigma with Total Quality Management applications, HR Functions, Lean Production, ISO 9000 and 9001
WE MAY CONCLUDE BY SAYING…..
“Six sigma would remain as one of the most likely key initiatives for improving the overall management process rather than just being remembered as one of the trends or fads.”
Six Sigma will move with a primary focus on improving overall management performance, rather than not just counting defects. With each passing day, a lot of effort is dedicated by researchers and practitioners to integrate six sigma with other existing innovative management practices so as to make six sigma method even more attractive to different organizations who have not started or fully implemented the six sigma methodology. The process of integration and comparison of six sigma principles and characteristics with that of Total Quality Management, Human Resource Functions, Lean Production, ISO 9000 and ISO 9001, the capability maturity model are all part of the quality community’s effort so as to capitalize on the positive effect of the six sigma method.
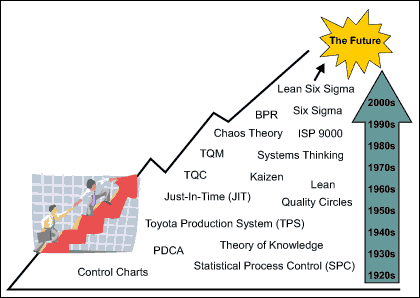