Roofs
The uppermost part of a constructed structure is called roof, provided to protect the building from rain, wind, snow, sun etc. It protects human beings, animals and also materials kept inside building. The roof should be strong, stable, weather proof and safe against fire and disaster.
Roofing Types, as per Shape
- Flat Roofs – Flat roofs have a slope from 1 degree to 5 degrees. These roofs are constructed in the same way as floor is. The roof acts much in the same way as a level plate form to support the load. This roof differs from intermediate floor in view of top finish called as ‘Terracing’. This terracing protects roof from adverse effects of rain, snow, heat etc.
- Pitched Roofs – Pitched roofs have a slope of more than 10 degrees to the horizontal Surface. The most common shape of roof is symmetrical pitched roof. The slope of roof varies according to the span, climatic conditions, types of roof covering etc. In areas of heavy snowfall, steeper slopes of 1: 1.5 or 1: 1 are provided to reduce incidence of snow load of roof. Pitched roofs are generally constructed of wood or steel. Steel trusses (frames) and rolled steel sections are used in construction of pitched roofs.
- Shell Roofs – Shell roofs are made to meet functional and architectural requirements. The roofs are provided in public buildings like libraries, theatres, recreation centers, factories or workshops etc. These roofs are used where large floor areas are required to be covered without obstruction from columns.
Roofing Types
- Concrete Roofing- Concrete tiles are widely used for roofing, as they have many advantages over other materials. In the early period, concrete was only considered as structural material used in the walls and roofs, but due to continuous experiments, concrete tiles were developed using fiber reinforced cement. There is a big variety of concrete roofing products including tiles and panels, but one thing is common among them, which is their strength, and durability. The cost of concrete tile is very low, which is almost half the clay tile cost. Some of them are made as replica of wood shingles or slates, which have more cost. Besides, if small tiles are used they cost much than the large tiles including both labor, and material cost.
- Iron Sheet Roofing – Generally corrugated galvanized iron sheets are extensively adopted as a covering for roofs and sides of industrial sheds and buildings. These are commonly available in length of 2.5 meter having a width of 900 mm and 1000 mm. The sheets are available in thickness of 0.63 mm to 1.60 mm. These sheets are coated with zinc. The sheets are cleaned, bright, free from rust, breakage etc. These should be according to IS: 270 class 2. Hooks, bolts, bitumen and steel washer, nuts and other accessories should confirm Indian Standard No.730.
- Steel Roofing – In past, steel roofing was not commonly used. However, steel roofing is gaining popularity because of its features. This roofing is durable, light in weight, maintenance-free, fire resistant and energy efficient. Steel roofing can be laid in many other style or shape of roofing. Steel is inherently a non explosive material and hence it’s resistant to fire. Radiant heat from the sun reflects the metal, which in turn reduces heat gain in the summer. In some cases to reduce the effect of heat from roof, foam and other insulation material may be fitted at the bottom of steel roofing. False ceiling is also provided under the steel roofing to give a good look and insulation. Steel roofing is available in tiles or slate.
- Clay Roof Tiles – Clay tiles show up mostly in homes with Italian and Spanish architecture, but the roofs of the modern buildings are also finished with this material. There is a big diversification of colors, styles, and types in clay roofing tiles.
- ACC Sheet Roofing – Asbestos cement sheet roofing should consist of either corrugated sheets or semi corrugated sheets as specified. The sheet should be of approved quality and shall confirm IS: 459. The sheet is free from cracks, chipped edges or corners and other damages. The slope of the roof is not less than 1 to 5. Normal slope adopted usually is 1 to 3.
Roof Maintenance
It’s critical that you inspect your roof every spring and fall. A good time to do this is when you’re cleaning your gutters.
- Look for missing, damaged or curling shingles and any other signs of wear and tear. It’s easy and inexpensive to replace one or two shingles, or to hire someone to do it for you.
- Check for signs of fungus or algae. If your roof is starting to collect moss or algae, install zinc or lead control strips.
- Inspect metal areas for rust. If it’s present, wire brush the rust, then prime and paint the metal.
- Examine the flashing to make sure it’s solid. If not, remove all of the old caulk and scrub the area clean before resealing.
- Seal any cracked mortar or caulking around joints and chimneys, if it appears to be deteriorating.
- If you see any signs of leaking, like dark spots on the ceiling, or mold or dampness in your attic, take action immediately. Roof leaks get worse, not better, and it’s better to spend a few dollars on roof maintenance rather than a lot on a big repair.
- Other roof maintenance issues
- Sweep or blow off excess debris on the roof. Sticks, leaves and other debris can damage shingles, cause algae to grow and eventually clog the gutters.
- Trim any branches that are hanging over the roof to prevent damage and keep squirrels and raccoons away.
- A thick layer of snow accumulation could lead to roof collapse. If this happens, carefully pull the snow off the roof using a snow rake available at most home improvement stores.
- Built-up roofs can also suffer from displaced or damaged surfacing. The surfacing is there to protect the waterproofing bitumen, so if strong winds are scouring off that protection, weathering will damage the waterproofing material and shorten the life of the roof. Fix this as quickly as possible, even if that only entails putting some roof mastic and gravel back on it until you can secure a lasting repair.
- Blisters can also affect modified bitumen, particularly older roofs utilizing SBS sheets in hot asphalt. Before 2004, the asphalt typically wasn’t hot enough to create proper bonding between the modified bitumen and the lower plies. Industry recommendations for the proper asphalt temperature have since eliminated the problem, but if your roof dates earlier than 2004, keep an eye out for blistering. Also watch for exposed modified membranes, which can fail in as few as five years if you live in a high-UV area. A coating can save your membrane if you catch the problem early enough, but when it’s badly degraded, the only solution is a new membrane.
- One of the biggest issues with single-ply roofs is open seams, so when you’re inspecting your roof, look carefully at all the seams. This type of roof has no redundancy, so if the roof fails, water has a direct path into your building. Single-ply sheets also tend to be thin, so dragging equipment or tools across the roof creates a split that allows water infiltration.
- Over time, you may spot raised fasteners on a single-ply roof. Fasteners are not typically set soundly or tightly, so building movement tends to cause the fasteners to back out and raise up. Excessive foot traffic can also lead to fastener trouble because it compresses the membrane and raises the load on the area with the fastener, which can then tear a hole in the membrane. When this happens, cut an X in the affected area, re-seat the fastener and put a patch on top.
- Raised fasteners can also affect metal roofs, though for different reasons. Fastened roof systems, such as structural metal roofs, pair fasteners with rubber gaskets. A fastener that isn’t fully seated into its gasket can allow water into the building. If the threading on the fastener is stripped, simply buy a larger diameter fastener and seat it properly.
- Corrosion is another concern for metal roofs. Copper coils in rooftop HVAC units produce condensate that contains both copper ions and acids, both of which will damage the zinc-based protective coatings on metal roofs and lead to rapid rusting. The damage can be catastrophic if you don’t catch it early enough. To prevent this from happening, duct the condensating water to keep it from running across the membrane. If you’re already noticing damage to the steel, look into new coatings to protect it from further deterioration.
Roof Leaks
Roof leaks weaken roof structure of the building and destroy household items also. They are irritating and most frustrating to the house owner. More than 90% of roof leaks are caused by improper installation and defective roof flashings.
Roof leaks create several problems as follows.
- Damages wall plaster and creates dry rot.
- Leads to increase the growth of molds and bacteria.
- Causes emission of chemical start from building materials.
- Destroys doors, windows, other timber items and household articles.
- Creates dampness which has adverse effects on the health of inhabitants of the house.
- Roof trusses and ‘Purlins’ starts rotting/rusting from continue exposure to dampness.
Detect Roof Leaks
- Inspect roof regularly and a couple of times during summer and spring seasons.
- Check blockage of rain water pipes and make sure if there is any debris in gutters or on roof. If it is found, clean that immediately.
- Ensure if there is any leakage in the joints of shingles with chimney, vent and skylights.
- Make sure loose fasteners are tight.
Repair defective portion of roof immediately. During repairs it is essential to look for any roof deterioration.
Causes of Leaks in Pitched Roof
- Faulty installation of roof or poor workmanship and inferior quality of materials used in construction of roof.
- Improper holes, broken or missing shingles, damaged gutter, vent or chimney surroundings.
- Heap of waste on roof or in the gutter prevents smooth flow of rain water which causes leakage.
- Weather effects such as high wind pressure, storm and heavy rain affect roof structure and cause leakage
Repair Leaks in Pitched Roof
- Make all gutters and roof clean – Clean the gutters for easy and quick flow of rain water. Clear all debris from the roof as it prevents easy flow of rain water and causes damage/ cracking of shingles or sheet due to the weight of debris. Keep rain water pipes clean and check them from time to time to prevent leakage.
- Mark actual area of leakage – Know actual causes of leakage and mark leakage area in daylight while it is raining. Take help from professionals in leakage treatment. Actual area of leakage should be calculated with the materials required for repair. The repair of roof leaks should be done before the beginning of rainy season.
- Tighten loose fasteners and inspect roof regularly – Check the roof after storm and if any fastener or hook is found loose, it should be tightened to avoid any further damage and leakage. Add extra fastener to the roof to avoid further damage to roof if the number of fasteners fixed are less.
- Replace missing or broken shingles\sheets – Repair gutters essentially and immediately as they provide direct access to drain off rain water from the roof. Replace missing or broken shingles/sheet at once by properly fixing them with necessary nails or J hooks. Restore defective or missing flashing with the joints of chimney, vent, gutter etc.
- Provide water proof outdoor silicone to prevent leakage – Remove old cracked sealant around the vent or chimney and fill it with proper quality outdoor silicone to prevent any leakage. Fill wrong and defective holes in roof shingles properly with water proof silicone material to avoid leakage through holes. Provide proper quality outdoor silicone to prevent leakage because the sealant around glass of skylight may crack over time and create leaks through the joints.
- Provide proper overlap – Give proper overlap and if any overlap of shingles or sheet is found improper, change defective, missing or cracked piece of shingle or sheet.
Repair leaks in flat roof
- Clean roof and check all rain water pipes – Clear all debris from the roof. Check all rain water pipes if there is any blockage in pipes as they provide direct access to rain water and repair defective joints of rain water pipes also.
- Mark actual area of leakage in daylight – Know actual causes of leakage and mark leakage in daylight while it is raining. Take help from professionals in leakage treatment. Actual area of leakage should be calculated with the materials required for repair. The repair of roof leaks should be done before the beginning of rainy season.
- Repair Tar felt water proofing coat and cement concrete ‘gola’ – Repair Tar felt water proofing coat if it is damaged and restore damaged cement concrete ‘gola’ in junction of wall and roof slab.
- Keep proper slope of tile tracing for smooth flow of rain water – Check the surface of roof and keep the slope of tile terracing in 1:40 ratio to drain off rain water quickly and to avoid leakage. Restore defective joints and repair depressions existing on the top of roof to avoid stagnant rain water which leads to leakage.
- Restore the joints of tile tracing – Mend the joints of tile terracing if they are cracked and repair defective/damaged cement pointing to avoid leakage.
- Check mouths of rain water pipes – Restore the mouth of rain water pipes and repair their cracked joints with tile terracing to avoid leakage.
- Repair leakage in overhead water tank – Repair leakage in overhead water tank; which destroys water proofing of roof. Fit proper ‘Bal’ cock and over flow pipe in overhead water tank to avoid unnecessary over flow of water which damages the roof.
Ceiling
A ceiling is an overhead interior surface that covers the upper limits of a room. It is not generally considered a structural element, but a finished surface concealing the underside of the roof structure or the floor of a storey above.
The most common type of ceiling is the dropped ceiling which is suspended from structural elements above. Pipework or ducts can be run in the gap above the ceiling, and insulation and fireproofing material can be placed here. Other types of ceiling include the cathedral ceiling, the concave or barrel-shaped ceiling, the stretched ceiling and the coffered ceiling. Coving often links the ceiling to the surrounding walls. Ceilings can play a part in reducing fire hazard, and a system is available for rating the fire resistance of dropped ceilings.
Ceilings are classified according to their appearance or construction. A cathedral ceiling is any tall ceiling area similar to those in a church. A dropped ceiling is one in which the finished surface is constructed anywhere from a few inches or centimetres to several feet or a few metres below the structure above it. This may be done for aesthetic purposes, such as achieving a desirable ceiling height; or practical purposes such as acoustic damping or providing a space for HVAC or piping. An inverse of this would be a raised floor. A concave or barrel-shaped ceiling is curved or rounded upward, usually for visual or acoustical value, while a coffered ceiling is divided into a grid of recessed square or octagonal panels, also called a “lacunar ceiling”. A cove ceiling uses a curved plaster transition between wall and ceiling; it is named for cove molding, a molding with a concave curve. A stretched ceiling (or stretch ceiling) uses a number of individual panels using material such as PVC fixed to a permieter rail.
False Ceilings
False ceiling is provided below the roof slab on suspended supports. The false celling is usually provided for temperature control (heat insulation for AC), to install lights, or to conceal electrical and other networking cables and ugly or too high ceiling. They are fixed to a framework suspended from main structure thus forming a void between the two components. The basic functional requirements of suspended ceilings are:
- They should be easy to construct, repair, maintain and clean.
- So designed that an adequate means of access is provided to the void space for the maintenance of the suspension system, concealed services and/or light fittings.
- Provide any required sound and/or thermal insulation.
- Provide any required acoustic control in terms of absorption and reverberation.
- Provide if required structural fire protection to structural steel beams supporting a concrete floor and contain fire stop cavity barriers within the void at defined intervals.
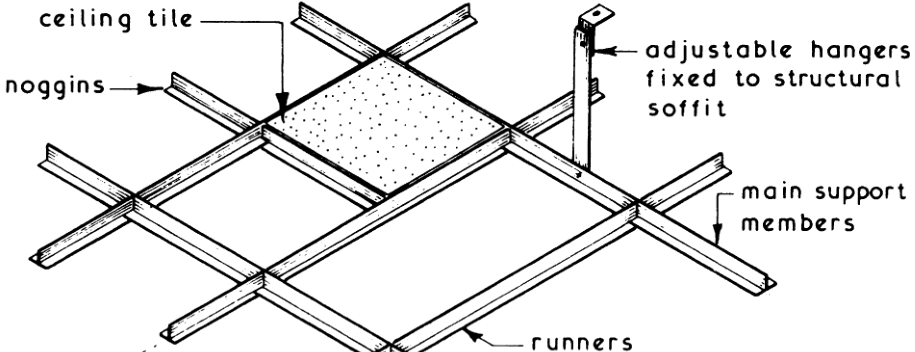
Types of False Ceiling: False ceilings can be differentiated into many types based on their uses, material used and appearance and visibility. The major classification based on materials used are
- Gypsum False Ceiling: Gypsum false ceiling is a hydrated sulfate of calcium. This type of false ceiling are lightweight, sound insulated, fire resistance, soft and thermally insulated. Gypsum false ceiling comes in the shape of square boards that are hung with the help of iron framework. The finishing work on these boards like paints, laminates, wallpapers and texture finish gives good look.
- Plaster of Paris Ceiling: Plaster of Paris (POP) is the majorly used material in the construction of false ceiling. POP is obtained when gypsum is heated to a certain degree. It gives the both aesthetical and functional help. Plaster of Paris false ceiling are attractive, almost no maintenance and has a long life span. They are very excellent insulators or heat and cold. These types of false ceiling don’t only hide the ugly members of structure, ventilation ducts and conduits but also give smooth finish to the ceiling.
- Fiber False Ceiling: Fiber false ceiling are in high demand for the construction of false ceiling due to low cost and east installation. The material used to manufacture fiber ceiling panels are man made by synthetic and natural minerals. As these are man-made they come in many shapes and sizes.
- Wooden False Ceiling: Wooden false ceiling is used due to its natural textures and pattern. Nowadays this types of false ceiling are used commonly as it gives a pleasant look to the eyes. Wooden false ceiling being costly, is not used in malls and hospitals but can be installed in residential buildings. They can be given various finishes, or painted to get the right look.
- Glass False Ceiling: One of the type of false ceiling used in construction are of glass. It is a non-crystalline material with the property of brittle and transparent. But this can be altered to make it non brittle and non-transparent using some admixtures. As glass is a good insulator of heat, it can be used for false ceiling. This type of false ceiling improves aesthetical appearance of the building.
- Metal Ceiling: As metal is a hard and durable material, it is used extensively in the false ceiling. When the metal surface is polished it gives a shiny surface which is a treat for eyes. The metals used in this are galvanized iron and aluminum. The cost of this ceiling are low as they are easy to install and access. The hidden members of the structure are easily accessed as the panels are easily removable and reattached. The construction cost becomes less as the installation, fixing and maintained is low.
- Synthetic Leather or Cloth Ceiling: The materials used in this type of ceilings are either leather or cloth. As both the used materials are man-made they can be given any form, shape and design which improves the aesthetic view of interior of the building. As these collects dust and has low light transferring property it’s only used in temporary tents or other temporary buildings.
Most suspended ceiling types can be placed in one of three groups
- Jointless Suspended Ceilings ~ these forms of suspended ceilings provide a continuous and jointless surface with the internal appearance of a conventional ceiling. They may be selected to fulfill fire resistance requirements or to provide a robust form of suspended ceiling.
- Panelled Suspended Ceilings ~ these are the most popular form of suspended ceiling consisting of a suspended grid framework to which the ceiling covering is attached. The covering can be of a tile, tray, board or strip format in a wide variety of materials with an exposed or concealed supporting framework. Services such as luminaries can usually be incorporated within the system.
- Decorative and Open Suspended Ceilings ~ these ceilings usually consist of an openwork grid or suspended shapes onto which the lights fixed at, above or below ceiling level can be trained thus creating a decorative and illuminated effect. Many of these ceilings are purpose designed and built as opposed to the proprietary systems associated with jointless and panelled suspended ceilings.
Ceiling Maintenance
Proper ceiling maintenance improves Indoor Air Quality. Even under the very best conditions ceilings should be cleaned and sanitized at least once every five years, even if they still look decent. Ceilings, especially porous acoustical ceiling tiles, act as sponges absorbing grease, germs, bacteria, mold, mildew, dust, smoke, nicotine, allergens, microorganisms and other air pollutants causing a reduction in Indoor Air Quality and discoloration of the ceiling surface. Professional ceiling cleaning and sanitizing removes all these hazards and leaves the ceiling bright and clean.
- Water Stains – Repairing water damage also comes under the heading of ceilng maintenance. Water stains do not always come out by cleaning. You should use a stain sealer to hide the water stains that are still noticeable after the cleaning process is complete.
- Grid Capping – If your grid system (the parts that hold up your tiles) is rusted or the paint is peeling it can be re-painted or covered with grid capping. Grid capping is made of a durable vinyl, is white, easy to clean, never rust or peels and is easily installed.
- Resurfacing Acoustical Tiles – Instead of painting you can resurface your acoustical tiles. A resurfacer restores your tiles to their original appearance. You can even change the color if you want. It is a non-toxic and faster drying alternative to paint. It is sprayed onto your ceiling in much the same way that paint is applied. A good resurfacing product will improve the noise reduction ability, has a class A fire rating and improves your ceiling tiles light reflection ability. The tiles will not stick to the grids. The grids and vents also get coated so the ceiling looks like it’s new. If you have warped or broken tiles these will need to be replaced.
- Remove dust or loose dirt with a brush or vacuum with an attachment used for upholstery. Always clean in one direction to avoid rubbing dirt or debris into the tile.
- Remove pencil marks, smudges, and stubborn dirt with an ordinary art gum eraser.
- Use fresh, good grade wall cleaner to tackle stubborn spots.
- Most mineral fiber and fiberglass ceilings may be cleaned with a damp cloth or sponge and mild soap. Use as little water as possible and wipe the soapy film off with a clean, damp cloth or sponge. *Please note that this cleaning method does not apply to cloth-faced ceiling panels.
- Some ceilings can withstand scrubbing, moisture and germicidal cleaners. Be sure to read the performance features of your specific ceiling.