Facilities layout refers to an optimum arrangement of different facilities including man, machine, equipment, material etc. Since a layout once implemented cannot be easily changed and costs of such a change are substantial, the facilities layout is a strategic decision. A poor layout will result in continuous losses in terms of higher efforts for material handling, more scrap and rework, poor space utilization etc. Hence, need to analyze and design a sound plant layout can hardly be over emphasized. It is a crucial function that has to be performed both at the time of initial design of any facility, and during its growth, development and diversification.
The problem of plant layout should be seen in relation to overall plant design which includes many other functions such as product design, sales planning, selection of the production process, plant size, plant location, buildings, diversification etc. The layout problem occurs because of many developments including:
- Change in product design
- Introduction of new product
- Obsolescence of facilities
- Changes in demand
- Market changes
- Competitive cost reduction
- Frequent accidents
- Adoption of new safety standards
- Decision to build a new plant
Plant layout problem is defined by Moore (1962) as follows:
“Plant layout is a plan of, or the act of planning, an optimum arrangement of facilities, including personnel, operating equipment, storage space, materials-handling equipment, and all other supporting services, along with the design of the best structure to contain these facilities.”
Objectives and Advantages
Some of the important objectives of a good plant layout are as follows:
- Overall simplification of production process in terms of equipment utilization, minimization of delays, reducing manufacturing time, and better provisions for maintenance
- Overall integration of man, materials, machinery, supporting activities and any other considerations in a way that result in the best compromise
- Minimization of material handling cost by suitably placing the facilities in the best flow sequence
- Saving in floor space, effective space utilization and less congestion/confusion
- Increased output and reduced inventories-in-process.
- Better supervision and control.
- Worker convenience, improved morale and worker satisfaction
- Better working environment, safety of employees and reduced hazards
- Minimization of waste and higher productivity Avoid unnecessary capital investment
- Higher flexibility and adaptability to changing conditions
Types of Layout Problems
The facilities layout problems can be classified according to the type of facility ° under consideration e.g.
- Manufacturing Plants
- Commercial facilities, e.g., shops, offices, Bank etc
- Service facilities, e.g., Hospitals, Post Offices etc
- Residential facilities, e.g., houses, apartments etc
- Cities, townships
- Recreational facilities, e.g. parks Theatres etc
According to the nature of layout problem, it can be categorized into four types as follows:
- Planning a completely new facility
- Expanding or relocating an existing facility
- Rearrangement of existing layout
- Minor modifications in present layout
Flow Patterns
According to the principle of flow, the layout plan arranges the work area for each operation, or process so as to have an overall smooth flow through the production/service facility. The basic types of flow patterns that are employed in designing the layouts are I-flow, L-flow, U-flow, 0-flow, S-flow as shown in Figure 1. These are briefly explained below:
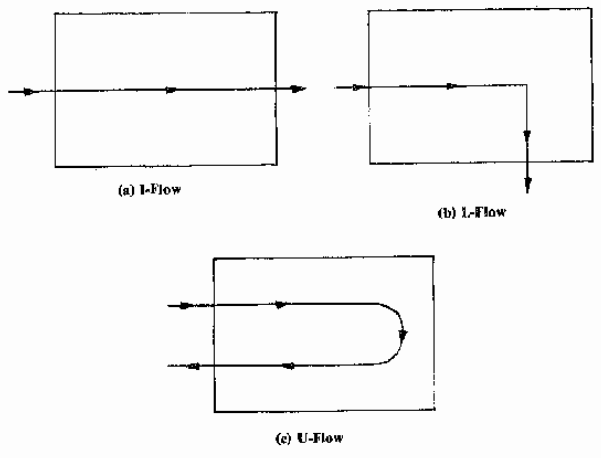
I-Flow: separate receiving and shipping area.
L-Flow: when straight line flow chart to be accommodated.
U-Flow: very popular as a combination of receiving and shipping.
O-Flow: when it is desired to terminate the flow near where it is originated.
Serpentine or S-Flow: when the production line is long and zigzagging on the production floor is required.