Depending upon the focus of layout design there are five basic or classical types of layouts. Most of the practical layouts are a suitable combination of these basic types to match the requirements of activities and flow. The basic types of the layouts are:
Product or Line Layout
This type of layout is developed for product focused systems. In this type of layout only one product, or one type of product, is produced in a given area. In case of product being assembled, this type of layout is popularly known as an ‘assembly line’
The work centers are organized in the sequence of appearance. The raw material enters at one end of the Line and goes from one operation to another rapidly with minimum of work-in-process storage and material handling. A typical product layout is shown in Figure II (a).
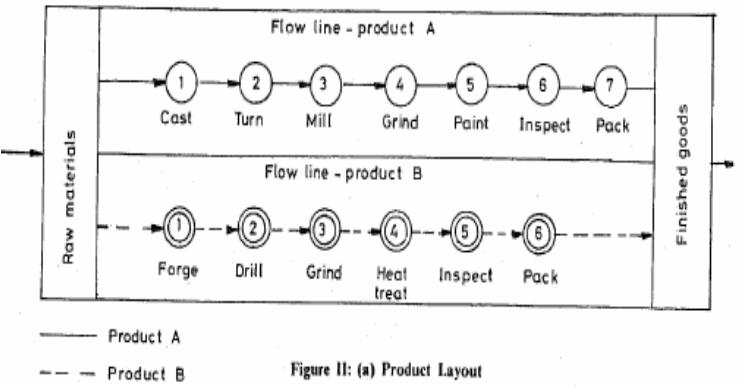
The decision to organize the facilities on a product or line basis is dependent upon a number of factors and has many consequences which should be carefully weighed. Following conditions favour the decision to go for a product focused layout.
- High volume of production for adequate equipment utilization
- Standardization of product and part interchangeability
- Reasonably stable product demand
- Uninterrupted supply of material
The major problem in designing the product-focused systems is to decide the cycle time and the sub-division of work which is properly balanced (popularly known as line balancing).
Some of the major advantages of this type of layout are:
- Reduction in material handling
- Less work-in-process
- Better utilization and specialization of labour
- Reduced congestion and smooth flow
- Effective supervision and control
Process or Functional Layout
This type of layout is developed for process focused systems. The processing units are organized by functions into departments on the assumption that. Certain skills and facilities are available in each department. Similar equipments and operations are grouped together, e.g., milling, foundry, drilling, plating, heat treatment etc. A typical process layout is shown in Figure II (b)
The use of process-focused systems is very wide both in manufacturing and other service facilities such as hospitals, large offices, municipal services etc.
The functional layout is more suited for low-volumes of production (batch production) and particularly when the product is not standardized. It is economical when flexibility is the basic system requirement. The flexibility may be in terms of the
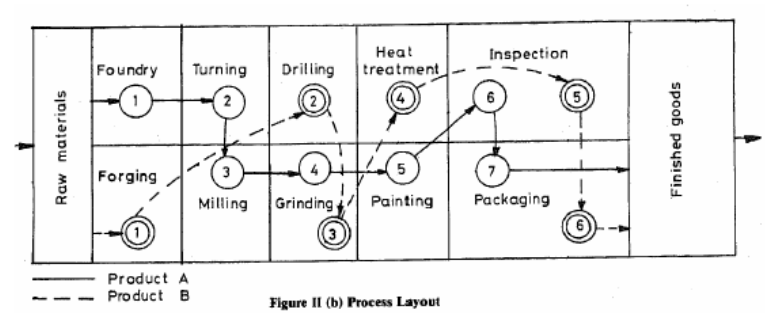
Routes through the system, volume of each order, and the processing requirements of the ‘items.
The major advantages of a process layout are:
- Better machine utilization
- Higher flexibility
- Greater incentive to individual worker
- More continuity of production in unforeseen conditions like breakdown, shortages, absenteeism etc
Cellular or Group Layout
It is a special type of functional layout in which the facilities are clubbed together into cells. This is suitable for systems designed to use the concepts, principles and approaches of `group technology’. Such a layout offers the advantages of mass production with high degree of flexibility. We can employ high degree of automation even if the number of products is more with flexible requirements. In such a system the facilities are grouped into cells which are able to perform similar type of functions for a group of products. A typical cellular layout is shown in Figure II (c).
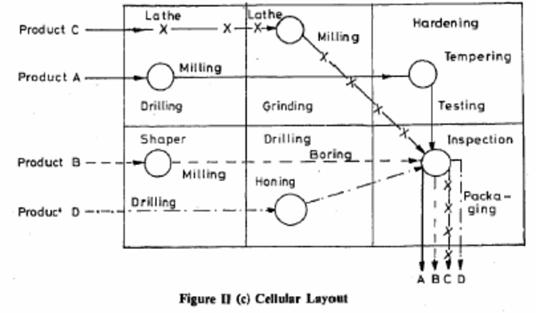
Job-shop Layout
It is a layout for a very general flexible system that is processing job production. The preparation of such a layout is dependent on the analysis of the possible populations of orders and is a relatively, complex affair.
Project or Fixed Position Layout
This is the layout for project type systems in which the major component is kept at a fixed position and all other materials, components, tools, machines, workers etc. are-brought and assembly or fabrication is carried out. This type of layout is now not used very commonly as the machines required for manufacturing work are big and complicated. The fixed position layout is used only when it is difficult to move the major component and fabrication is to be carried out e.g. production of ships.
Some of the major advantages of fixed position layout are as follows:
- The handling requirements for major unit are minimized.
- Flexible with reference to the changes in product design
- High adaptability to the variety of product and intermittent demand
- The responsibility for quality can be pin-pointed.
- The capital investment is minimum
A typical fixed position layout is shown in Figure II (d).
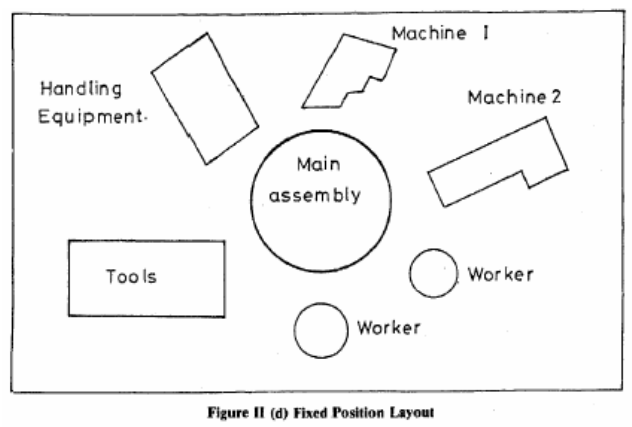
Activity B
Can you identify the basic type of plant layout in the facility you work in? Is it optimal? Would some other type of layout than the one currently prevailing in your facility be better?
The fixed position layout is used ideally for a project situation i.e. for one product of a different type. As the quantity increases the production operations can be broken down into different work centres and material can be allowed to move rather than the machines and a process layout is preferred. With further increase in volume i.e. with mass production the advantages of production line can be better derived and a product layout is desirable. The break-even analysis comprising the production volume of the three basic layouts i.e., product, process and fixed position layout is shown in Figure III.
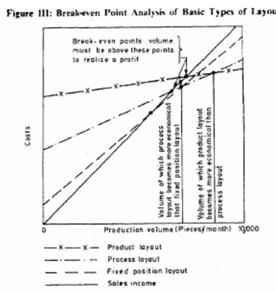