On the basis nature of operations the organisations can be divided in to:
- Manufacturing organisations
- Non-manufacturing organisations
The following are the differences between manufacturing organisations and non-manufacturing organisations:
- Manufacturing organisation produces the goods that are tangible in nature. On the other hand service organisations render service to the customers instead of tangible products.
- The products of manufacturing units can be stored in physical form. But the products of non-manufacturing organisation cannot be stored.
- In manufacturing organisation, most of the customers have no direct contact with the operations. On the other hand, in the case of service organisations the customers are present during the creation of the service.
Differences between the goods and the service
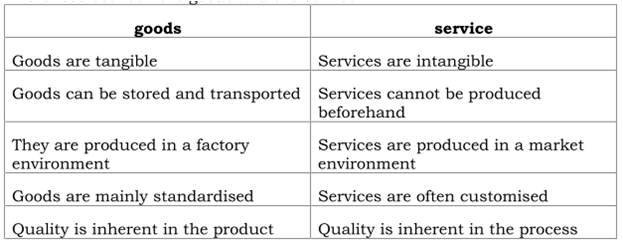
Service and manufacturing operations have differences, but also similarities. For example, both create mission statements and a vision for how the organization will be run and perceived by customers. Each provider or manufacturer wants to lead the market in its specific industry. However, manufacturing and service operations answer different questions and formulate different strategies when it comes to planning and managing the way in which an organization is run.
Characteristics
Manufacturing operations produce tangible goods, which are physical products that can be held and seen. Manufacturing can be broken down into two branches: process and discrete manufacturing. While process manufacturers produce goods that typically use a formula and ingredients, such as soda pop or pharmaceutical drugs, discrete manufacturers produce goods from parts, such as electronics, appliances and automobiles. On the other hand, service operations provide certain intangible services that may not be easily identifiable. Service operations can be classified into many industries, such as banking, hospitality, advertising and consultancy.
Customization vs. Standardization
In general, manufacturers have a standardized way of producing goods. Goods are produced en masse in a factory or warehouse-type environment. One finished product is generally the same as the next. Service operations, by contrast, have more opportunities to customize the services they provide. For example, beauticians and hairdressers must customize the styling and treatments to match the customer’s hair, shape of face and other characteristics. Even in service operations where you receive a tangible product, the service you receive from workers may not always be the same.
Production Environment
Manufacturing and service operations both plan the environment in which work takes place, but they focus on different elements. Manufacturing operations, for instance, consider the manufacturing layout. For example, the manufacturing layout can be fixed, process-focused or product-focused, such as in an assembly line factory. These issues affect the manufacturer’s workforce performance and total output. Service operations, by contrast, plan the environment according to how it affects customers. For example, service operations are concerned with how the atmosphere appears to customers. Dimensions of the service environment include the layout of furnishings, arrangement of signs and tangible cues, such as colors and sounds designed to enhance the customer experience.
Operations Management
In a manufacturing environment, operations managers oversee the activities required to produce goods from raw materials. Issues managers in this environment face include managing the space to store raw materials, the flow of materials through the manufacturing process, how much product to produce and quality of output. In a service operation, operations managers schedule workers to handle customer demand. They must coach and train employees to provide optimal services to customers. Service operations that also sell physical goods also face inventory control issues, such as how much to stock and when to order.
Similar Issues
Service and manufacturing organizations face many similar issues that affect the end result of the operation. For example, both face issues of cost control. Manufacturing operations must find suppliers of raw materials at the lowest cost — and highest quality — possible. Likewise, service operations’ indirect cost of providing services must be kept low so that the organization can provide competitive prices to customers and still turn a profit. Other issues both types of operations face include forecasting demand for products and services and staying competitive in the marketplace.
Overlap
In the past, managing service operations and managing manufacturing operations have been considered opposites. But in modern economies, manufacturing and services seem to be interdependent and overlapping.
Also, while manufacturers are traditionally supposed to be exclusively making tangible products, computer manufacturers, for example, may also offer such intangibles as after-sales services and technical support. And even organizations that are more exclusively service oriented will often have elements that do not have the traditional service characteristics. For instance, while services are traditionally characterized by high levels of contact with clients, back-office employees in service organizations have little, if any, contact with clients. It’s also not always true that service organizations are more labor intensive than capital intensive. Innovations in technology have reduced the labor intensiveness of many service organizations. For example, ATMs have reduced the need for human tellers in banks.
Some organizations are hard to categorize as service or manufacturing. For instance, a shipping company will have characteristics of both. A key output in this case is an intangible service – the reliable delivery of documents and packages. But, like traditional manufacturing businesses, such companies will be characterized by minimal customer contact and high capital intensiveness in terms of facilities and fleets of vehicles.