Stores Accounting Systems
Stores accounting is important from the point of view of estimating the cost of the product for pricing decisions. The costing of material has to be done both for the materials consumed in the production and estimating the value of materials held in stock.
For the purpose of costing the receipt of materials, the factors that should be included are material price, freight charges, insurance, duties, taxes, packaging charges etc. The prices quoted and accepted in purchase order may often be stated in various ways such as net prices, prices with discount terms, free on board, cost, insurance, freight, etc. All these factors should be appropriately accounted while costing for the incoming materials.
Another important accounting is to be done for the issue to production and of the stocks held at the end of accounting period. Let us discuss some of the important and frequently used system for this purpose:
FIFO System: This system known as First in First Out System is based on the assumption that the oldest stock is depleted first. Therefore, at the time of issue the rate pertaining to that will be applied. There is no `profit’ or `loss’ in the pricing arrangements. The value of the stocks held on hand is the money that has been paid for that amount of stock at latest price levels. In case of too many changes in price levels the FIFO System becomes unwieldy. Another limitation of this system is that it fails to provide a satisfactory answer to costing-returns from stores.
LIFO System: This system known as `Last in First Out’ System is based on the assumption that the most recent receipts are issued first. As the latest prices are charged in this system, it leads to lower reported profits in the periods of rising prices and this offers savings in taxes. In case of wide fluctuations in prices this system tends to immunize unrealized gains or losses in inventory. It has almost the same limitations as that of FIFO System.
Average Cost System: This is based on the assumption that issues to production department are equally made from different shipments in stock, i.e. an average cost of shipment in stores is charged. It stabilizes the cost figures. The average is to be calculated by dividing the total cost with the number of items and is to be updated with every new purchase.
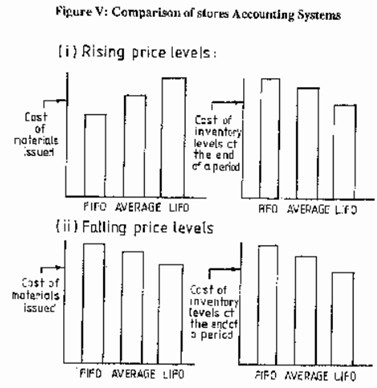
Market Value System: This is also known as replacement rate costing, in which the materials issued are charged the prevailing market rates. This system underestimates the stock on hand in the case of price increase, whereas it overestimates the stock on hand in the case of price decrease. This may in turn lead to writing off huge amount to make it realistic. Moreover, a continuous monitoring of the market rates for all materials makes the system cumbersome.
Standard Cost System: In this system a detailed analysis of market price and trends is carried out to determine a standard rate for a fixed period, say six months or so. This standard rate is charged to materials issued during this period irrespective of the actual rate. After the period is over the standard rate is reviewed and updated.
This system reflects the efficient use of materials as the fluctuation in rates is not considered in accounting. Moreover, it adds to clerical efficiency as the fresh rates are not to be obtained every time. However, similar to Market Value Approach, this also leads to underestimating or overestimating stocks on hand in case of rising and falling prices respectively.
System of Costing the Closing Stock: The general guideline for this purpose is to use market price or stock at cost, whichever is less.: The cost of closing stock is governed mainly by price units, obsolescence and deterioration. In rare cases the stock may appreciate with time. Appropriate formulae to account for these factors should be developed keeping in view the past experience.
Stock Verification Systems
Some discrepancies between the actual and the book balances of inventories are bound to occur despite the diligent store keeping. The process of stock verification is carried out for following purposes:
- To reconcile the store records and documents for their accuracy and usefulness,
- Identification of areas deserving tighter document control,
- To back-up the balance sheet stock figures, and
- To minimize the pilferage and fraudulent practices
Most companies keep an “inventory short and over” account to absorb such discrepancies, which is eventually closed into the manufacturing overheads account. Some of the systems of physical stock taking are as follows:
Annual or Periodic Physical Verification: In this system the entire inventory is physically verified at the end of a period, usually the accounting period. That is, normally at the end of fiscal year. Stocks are closed for a few days. This may necessitate the shutdown of production operations;.’ the activities such as repair and overhaul of equipment and machinery are resorted to. A special crew of store inspectors and stores verifying officers, usually from the material audit, physically check each item and compare the entries on bin card and stores ledger. This leads to the formation of a list of surplus or short items. Damaged and obsolete items are traced and recorded. This needs to develop a detailed programme and schedule to complete the verifications, store wise and item wise. Top management’s sanction can then be sought for writing off deficiencies or valuing surplus.
As all the items are checked at one time there can be no confusion about any item being left unchecked.
Perpetual Inventory and Continuous Stock Taking System: In case of large firms dealing with a large number of items the final inventory system may take a lot of time and it may not be possible to shut down the whole plant. The perpetual inventory system is a more appropriate method for large plants. In this method the stock verification is done continuously throughout the year. Different methods are adopted by different firms for continuous verification.
Some firms divide the whole inventory into fifty-two equal parts. Each part is verified every week. Some firms’ record store balances after every receipt and issue, and a number of items are counted daily or at frequent intervals and checked with the bin cards and stores ledger. Discrepancies found, if any, owing to incorrect entries, breakage pilferage, over-issue, placing of items in wrong bins, etc., are investigated and corrected accordingly. The significant advantages of this system are as follows:
The shutdown of the plant is not necessary for stock checking/taking.
- The method is less costly, less tiring, less cumbersome and hence is more accurate.
- Discrepancies and defects in stores are readily detected and are not carried over throughout the year. This prevents damages and losses.
- Slow moving stocks can be noted and proper action can be initiated in time. v) The stock items are kept within the limits.
Low Point Inventory System: Some companies take the physical inventory, i.e. the stock level of stores is checked generally when it reaches its minimum level.