Preventative maintenance (or preventive maintenance) is maintenance that is regularly performed on a piece of equipment to lessen the likelihood of it failing. Preventative maintenance is performed while the equipment is still working, so that it does not break down unexpectedly.
Preventative maintenance is planned so that any required resources are available.
The maintenance is scheduled based on a time or usage trigger. A typical example of an asset with a time based preventative maintenance schedule is an air-conditioner which is serviced every year, before summer. A typical example of an asset with a usage based preventative maintenance schedule is a motor-vehicle which might be scheduled for service every 10,000km.
Preventative maintenance is more complex to coordinate than run-to-failure maintenance because the maintenance schedule must be planned. Preventative maintenance is less complex to coordinate than predictive maintenance because monitoring strategies do not have to be planned nor the results interpreted.
Assets suitable for preventative maintenance include those that:
- have a critical operational function
- have failure modes that can be prevented (and not increased) with regular maintenance
- have a likelihood of failure that increases with time or use
Advantages of preventative maintenance
Advantages compared with less complex strategies – Planning is the biggest advantage of preventative maintenance over less complex strategies. Unplanned reactive maintenance has many overhead costs that can be avoided during the planning process. The cost of unplanned maintenance includes lost production, higher costs for parts and shipping, as well as time lost responding to emergencies and diagnosing faults while equipment is not working. Unplanned maintenance typically costs three to nine times more than planned maintenance. When maintenance is planned, each of these costs can be reduced. Equipment can be shut down to coincide with production downtime. Prior to the shutdown, any required parts, supplies and personnel can be gathered to minimize the time taken for a repair. These measures decrease the total cost of the maintenance. Safety is also improved because equipment breaks down less often than in less complex strategies.
Advantages compared with more complex strategies – Preventative maintenance does not require condition-based monitoring. This eliminates the need (and cost) to conduct and interpret condition monitoring data and act on the results of that interpretation. It also eliminates the need to own and use condition monitoring equipment.
Disadvantages of preventative maintenance
Disadvantages compared with less complex strategies – Unlike reactive maintenance, preventative maintenance requires maintenance planning. This requires an investment in time and resources that are not required with less complex maintenance strategies.
Maintenance may occur too often with a preventative maintenance strategy. Unless, and until the maintenance frequencies are optimized for minimum maintenance, too much or too little preventative maintenance will occur.
Disadvantages compared with more complex strategies – The frequency of preventative maintenance is most likely to be too high. This frequency can be lowered, without sacrificing reliability when condition monitoring and analysis is used. The decrease in maintenance frequency is offset by the additional costs associated with conducting the condition monitoring.
Recommended Best Practices
- Create an inventory of building components and inspect their condition
- Set priorities among maintenance projects and evaluate projects’ lifetime costs
- Plan and budget strategically for preventive maintenance in the long- and short-term
- Structure a framework for operating a preventive maintenance program, including checklists of preventive maintenance tasks
- Use tools, such as work-order systems, to optimize preventive maintenance program
- Ensure that maintenance employees have appropriate training to competently complete their tasks
- Involve appropriate maintenance personnel when designing space and purchasing building components.
PM Checklist
Use this checklist to keep major building systems – HVAC, roofing, plumbing and lighting – in good working order.
Roofing – Save yourself from recurring issues and unexpected failures by using a roof asset management program. This strategy syncs preventive maintenance and inspections with corrective action, ultimately extending the time between roof replacements.
- Inspect at least twice a year and after any severe storm.
- Create a roofing file for each building; review warranty information.
- Clear roof drains of debris (roof warranties don’t cover this).
- Walk the perimeter to examine sheet metal, copings, and previously repaired sections.
- Check roof-to-wall connections and examine flashings (at curbs and penetrations, etc.) for wrinkles and tearing.
- For single-ply roofs, re-caulk the top of face-mounted termination bars (if needed).
- For bituminous roofs, check for splits in the stripping plies.
- Be on guard against corrosion on metal roofs, which may be caused by condensate from copper coils in rooftop HVAC units. Duct the condensating water to keep it from coming into contact with the membrane.
- Keep traffic off of the roof to avoid membrane damage.
- Don’t let your green roof die from lack of care. Be attentive to plant health by monitoring growth and weeding and trimming as needed. Proper irrigation is not only critical for the survival of vegetation but also protects your roof membrane against leaks and ponding.
- Plan a moisture survey every 5 years to detect wet insulation or leaks.
- If you have a rooftop solar array, be aware that panels can become dislodged by a buildup of ice and snow. Inspect the racks and areas around penetrations during your regular walkthroughs. You can also mount ballasted systems on a pad to protect the roof membrane from possible damage.
HVAC – Maintaining heating and cooling equipment, helps to preserve energy efficiency and indoor air quality.
- Inspect at least twice a year, with seasonal start-up and run inspections. Look for screw or latch updates, gasket repairs, and missing screws replacements. Also recharge P-traps or U-bend water traps for condensate drain pans.
- Seasonal PM of chillers and boilers is involved; industry practice is to have a qualified mechanical contractor provide services.
- For cooling towers, disassemble screens and access panels for inspection; inspect the tower fill, support structure, sump and spray nozzles, fill valve, gear box, drive coupling, fan blades, and motor bearings; clean starter and cabinet; inspect wiring; check motor starter contacts for wear and proper operation; megger test the motor and log readings; and check the condition of the sump heater and contactor, and log observations.
- Pumps usually require bearing lubrication at least annually. Inspect couplings and check for leaks. Investigate unusual noises.
- Air handling unit maintenance should include cleaning or replacing air filters at least once a month, though some may only need to be changed every 3-6 months.
- If you can reach the condenser coil, simply buy coil cleaner, apply and wipe off. If you need to remove panels to access the coil, use a licensed contractor.
- Periodically inspect settings for energy efficiency, particularly the compressor, refrigerant charge and thermal expansion valve (if applicable).
- In direct pressure systems, confirm that the superheat temperature falls between 10-20 degrees F. Look up the evaporating temperature per the manufacturer that corresponds with the measured suction line pressure, then measure the actual suction line temperature – the difference between these two numbers is the superheat temperature.
Plumbing – A drip here and there may seem innocent, but leaks aren’t always visible to the naked eye. Start with bathrooms and explore larger building systems.
- Inspect at least annually; investigate any leaks or unusual noises.
- Domestic water booster and circulation pump systems require bearing lubrication at least annually; inspect couplings and check for any leaks.
- Domestic water heaters and boilers should be fire-tested periodically, using flue-gas analysis to adjust the flue draft and combustion air input to optimize efficiency.
- Remote drinking water chillers need condenser fan motor bearings lubricated annually. Check all contacts for wear and pitting, and run system control tests. Pump down the system and remove the refrigerant according to manufacturer instructions. Drain and replace oil in the compressor oil reservoir, including filters, strainers, and traps.
- Sump and sewage ejection pumps are replaced on an as-needed basis but should be checked for function. Exposed pumps should be lubricated annually.
- Fixtures, particularly those in public restrooms, often withstand heavy use and abuse. Check for leaks regularly and follow the manufacturer’s recommendations on how often to replace internal workings such as flappers, cartridges and diaphragms.
Lighting – Haphazardly maintained fixtures can fail to deliver energy savings and lower light quality.
- Inspect at regular intervals, with group relamping when lamps begin to fail.
- Routinely check any luminaires that have transformers, control gear, or accessories, such as spread lenses, glare baffles, or color filters.
- Check exterior lights to make sure cables aren’t torn; all screws and hardware should be in place and working, and gaskets can be replaced to provide a better watertight seal.
- Replace any burned-out lamps and consider group relamping. To create your relamping schedule, calculate lamp life and how often lamps are used.
- Re-aim adjustable lighting as necessary.
- Dust lamps and clean lens surfaces to enhance lighting performance.
- Because lighting elements can contain mercury or lead, it’s imperative to safely store used bulbs until they can be removed.
Long Term Items – Electrical systems should be inspected by a licensed electrician every 3 to 5 years; PM typically includes checking switchgear, panel boards, and connections in addition to cleaning and re-torquing electrical connections. Overcurrent devices should be cleaned and lubricated as required; fusible switch units should be checked to make sure all fuses within the unit are from the same manufacturer and of the same class and rating. Note that arcing failures occur where connections have been loosened as a result of thermal cycling.
Surfaces in parking garages should be cleaned at least twice a year, with coating replacement every 10 years. Power washing is a cheap, easy way to protect the structure and delay rehabilitation projects. Pavements should be crack-filled and seal-coated on a regular basis. Mill and overlay pavements should be done every 20 years.
Continuum of Maintenance for Buildings
Preventive maintenance means the regularly scheduled repair and maintenance needed to keep a building component operating at peak efficiency and extend its useful life.
It includes scheduled activities intended to prevent breakdowns, such as periodic inspections, lubrication, calibrations, and replacement of equipment. Replacing filters in an air-handling unit on a regularly scheduled basis is an example of preventive maintenance. Because prolonging the life of major building systems requires periodic replacement of equipment, preventive maintenance typically requires both capital and operating expenditures.
A continuum of building maintenance is illustrated by figure below. At one end is deferred maintenance, which occurs when projects are identified as necessary but put off due to lack of resources. Next along the continuum are unplanned activities including emergency maintenance, such as restoring lost electrical power, and corrective maintenance, such as fixing a broken window. Emergency and corrective maintenance occur as the need arises; neither is planned far in advance.
Planned maintenance follows on the continuum, although the maintenance categories are not mutually exclusive. General maintenance is the upkeep of building components to restore them to their original conditions or to keep them in good working condition. Preventive maintenance follows on the continuum.
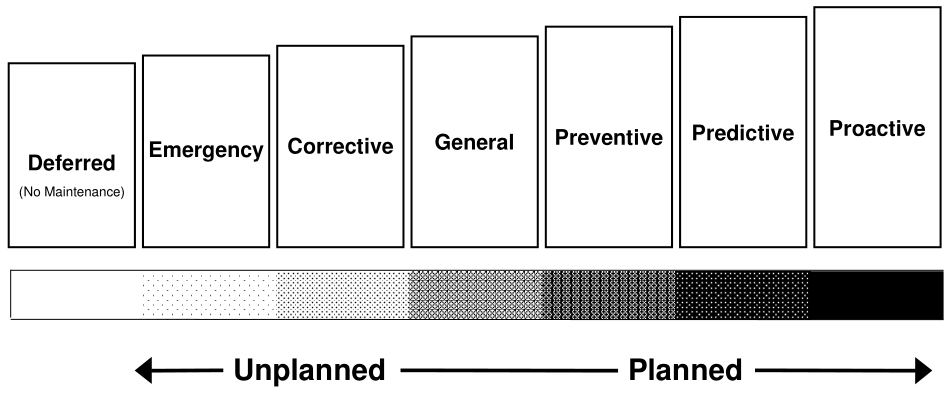
A step beyond that is proactive maintenance, a highly structured practice that uses information from analyzing equipment to identify origins, not just symptoms, of equipment problems. Proactive maintenance would, for example, identify whether excessive wear resulted from defective installation, unsuitable design, or some other cause. Because it addresses the root sources of equipment problems, proactive maintenance eliminates recurring problems and the downtime and other costs associated with those recurrences.
Value of Preventive Maintenance
Preventive maintenance is widely thought to reduce long-term costs by maximizing the operating capacities of equipment, minimizing downtime, and avoiding breakdowns that would otherwise lead to higher repair costs later.
For instance, the preventive maintenance tasks of cleaning coils and replacing dirty filters in a heating, ventilation, and air-conditioning (HVAC) system have shown reduced energy costs for running an HVAC of 8 to 10 percent. In a die-casting company that adopted preventive maintenance, equipment breakdowns went from being a common occurrence to constituting approximately 1 percent of scheduled operating time over a ten-year period. Further, maintenance efficiencies allowed the company to reduce its maintenance workforce from 15 to 8 employees during that time.
Also important are the potential effects of preventive maintenance on building occupants. Because of its impact on the condition of a building’s components, preventive maintenance may indirectly affect occupants’ productivity and health.
Maintaining good indoor air can have direct, positive effects on building occupants. As an example, one study quantified savings from improved worker productivity and health associated with making indoor air quality improvements
Steps to Creating a Preventive Maintenance Plan
Documentation
- Original construction drawings and specifications
- Building condition assessments
- Engineering studies on specific components such as elevators or parking garage
- Energy efficiency studies
- Fire safety plan
- Renovation, refurbishment, retrofits or other capital
- Operating manuals and maintenance instructions
- Warranties
- Current service orders
Inspection
- Regular intervals
- All building areas
- Manager and Maintenance staff
- Develop observation skills
- Take pictures
Creating the PM Schedule
- Format: Make sure it works for you!
- Content: Be comprehensive
- Task Assignment: Who does what and when
Implementation
- Who does it? How? With what?: Staff training, supplies, contractors
- Communication, Accountability & Reporting