The production plan represents a firm’s aggregate measure of manufacturing output. Once this plan is made, it is the responsibility of marketing to sell it and production to implement it. To do so requires a desegregation of the production plan into individual products. The master production schedule (MPS) is a statement of how many finished items are to be produced. Typically the master schedule is developed for weekly time periods over 6-12 months horizon.
Master scheduling is generally a complex problem, especially for products with large number of operations For example, in Dow Corning there are 12 MPS; who are responsible for scheduling 400 packed products over a 26-week time horizon. In process industries with only a few different operations, master production scheduling is somewhat easier.
A master production schedule (MPS) is a plan for individual commodities to be produced in each time period such as production, staffing, inventory, etc. It is usually linked to manufacturing where the plan indicates when and how much of each product will be demanded. This plan quantifies significant processes, parts, and other resources in order to optimize production, to identify bottlenecks, and to anticipate needs and completed goods. Since an MPS drives much factory activity, its accuracy and viability dramatically affect profitability. Typical MPSs are created by software with user tweaking.
The MPS is a statement of what the company expects to produce and purchase (i.e. quantity to be produced, staffing levels, dates, available to promise, projected balance). The MPS translates the customer demand (sales orders, PIR’s), into a build plan using planned orders in a true component scheduling environment. Using MPS helps avoid shortages, costly expediting, last minute scheduling, and inefficient allocation of resources. Working with MPS allows businesses to consolidate planned parts, produce master schedules and forecasts for any level of the Bill of Material (BOM) for any type of part.
The main functions of MPS are:
- To translate aggregate plans into specific end items: Aggregate plan determines level of operations that tentatively balances the market demands with the material, labour and equipment capabilities of the company. A master schedule translates this plan into specific number of end items to be produced in specific time period.
- Evaluate alternative schedules: Master schedule is prepared by trial and error. Many computer simulation models are available to evaluate the alternate schedules.
- Generate material requirement: It forms the basic input for material requirement planning (MRP).
- Generate capacity requirements: Capacity requirements are directly derived from MPS. Master scheduling is thus a prerequisite for capacity planning.
- Facilitate information processing: By controlling the load on the plant. Master schedule determines when the delivery should be made. It coordinates with other management information systems such as, marketing, finance and personnel.
- Effective utilization of capacity: By specifying end item requirements schedule establishes the load and utilization requirements for machines and equipment.
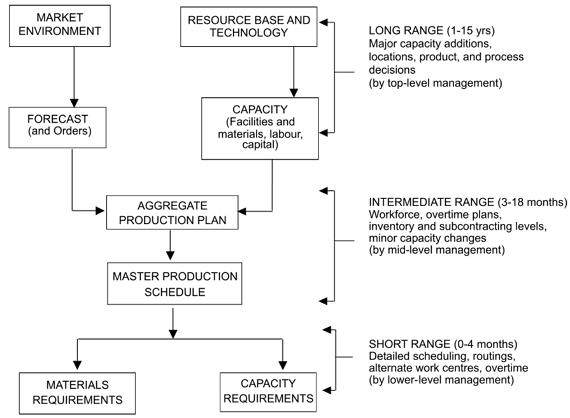
MPS Attributes
- The MPS is a statement of the specific products that make up manufacturing output
- The MPS is a translation of the sales and operations plan into producible products with their timing and quantities determined
- The MPS shows when products will be available in the future
- The MPS is a statement of production, not of demand
- The MPS is not a forecast
- The MPS considers factors such as capacity constraints, costs of production, resource limitations, and the sales and operations plan
- The MPS is stated in terms of product specifications–usually part numbers which have specific bills of materials (BOM)
- In assemble-to-order environments, the MPS may be stated in terms of an “average” final product
- In a make-to-stock company, the MPS is a statement of how much of each end item to be produced and when it will be available
- In a make-to-order (or engineer-to-order) firm, the MPS is usually defined as the specific end item(s) that make up an actual customer order
- In an assemble-to-order firm, the large number of possible product combinations is represented with a planning bill of materials
Working
By using many variables as inputs the MPS will generate a set of outputs used for decision making. Inputs may include forecast demand, production costs, inventory money, customer needs, inventory progress, supply, lot size, production lead time, and capacity. Inputs may be automatically generated by an ERP system that links a sales department with a production department. For instance, when the sales department records a sale, the forecast demand may be automatically shifted to meet the new demand. Inputs may also be inputted manually from forecasts that have also been calculated manually. Outputs may include amounts to be produced, staffing levels, quantity available to promise, and projected available balance. Outputs may be used to create a Material Requirements Planning (MRP) schedule.
A master production schedule may be necessary for organizations to synchronize their operations and become more efficient. An effective MPS ultimately will:
- Give production, planning, purchasing, and management the information to plan and control manufacturing
- Tie overall business planning and forecasting to detail operations
- Enable marketing to make legitimate delivery commitments to warehouses and customers
- Increase the efficiency and accuracy of a company’s manufacturing
- Rough cut capacity planning
MPS issues:
- Width of the time bucket
- Planning horizon
- Rolling plan
- Time fencing
- Schedule freezing
The Master Production Schedule is a detailed Plan of Production. It drives the MRP system by referencing inventory, requirements and bill of materials. For the purpose of Materials Requirements Planning, the time periods must be identical with those used in MRP system.
Master Production Schedule represents the plan for manufacturing products. It consists of quantities, dates and configurations. Typical MPS is a table containing the following information:
- Demand forecast
- Allocated, Reserved and Unplanned slots
- Planned Order – planned and firm
- Projected Available Balance (PAB)
- Available to promise (ATP)
Using the Master Schedule
Master scheduling can be a complicated process. Let us summarize some of the observations.
- First, the master production schedule should relate to the aggregate products.
- Second, rough-cut capacity planning assists the master scheduler in developing a feasible schedule by determining potential production bottlenecks. Often, the master scheduled must be revised several times until it is feasible.
- Third, other ways of evaluating a master production schedule include the and cost of setups or product changeovers and short-term inventory fluctuations.
The master schedule is important, since it forms the basis for future production planning activities. Therefore, it must be adaptive to changes in the environment. Seldom will forecasted demands be realized or production plans be adhered to perfectly. As each week passes, operations managers must compare scheduled production with actual results. This may result in changes to the MPS-master scheduling is a full time job! Too many changes, however, indicate that master scheduling is not being performed correctly and can result in poor productivity and low levels of customer service.