Optimization is an act, process, or methodology of making something (as a design, system, or decision) as fully perfect, functional, or effective as possible.
To help facility managers better review their operations (from workforce management to supplies), make strategic decisions that benefit the overall health of their buildings and maximize their workforce, Staples Advantage offers these helpful tips:
- Look at the Scope of Work: As a facility manger, start by taking a holistic view of your entire workforce and operations. By conducting this analysis, a facility manager can see where the team’s time is currently spent, which tasks are being completed and how often. Once there is a basic knowledge of where work is being conducted, a facility manager can evaluate or switch to higher quality products. Further, by evaluating productivity rates and how often tasks are being performed, a facility manager can see which areas can be cleaned less frequently (e.g. once a week vs. once a day). This will help free time for employees to focus on more important tasks.
- Assess Risk Levels: Cleaning has always focused on health and reducing risk for those entering a building. As such, facility managers need to assess risk levels throughout their facility and allocate team members appropriately. For example, in a hospital, a surgical room is at a higher risk for contamination than the office areas. To preserve occupant health, different cleaning measures and higher precautions will need to be taken. The facility manager should determine the right products and the frequency in which to use them, and distribute more team members to focus on thoroughly cleaning these high risk areas.
- Evaluate Innovative Options: When conducting an audit, do not overlook sustainable options. These solutions, which take social, economic and environmental factors into account, should be viewed as cost neutral. In the long-term, they will often cost as much as, or less than traditional cleaning products. Also, it is important to mechanize some of the heavier lifting processes. For instance, try replacing a mop with an auto-scrubber. Effectively leveraging cleaning technology will lead to more streamlined cleaning processes, which will decrease costs in the long-term.
Preventive Maintenance Optimization
PM Optimization (PMO) is a structured process aimed at preserving and restoring the equipment condition. With PMO, we focus on identification of the failures (failure modes) and develop PM tasks to manage the failure.
Preventive Maintenance Optimization is a process to improve the effectiveness and efficiency of the PM process. Effective PMs address and reduce the consequence of specific, probable failure modes. Efficient PMs are value-added tasks conducted using the least labor, downtime, and materials required to complete the task.
How can we optimize our PMs? First let’s consider the origin of many PM programs. PMs are often hastily put in place to meet a requirement or project objective. They are often cut and pasted from other machine PMs or taken directly from the OEM manual. While these might be an okay starting point, there can be a significant issue if they are left unchanged over a period of time.
PM Optimization is built upon a series of key concepts and structured processes. Some Preventive Maintenance Optimization processes are very rigid and closely follow Reliability-Centered Maintenance (RCM) process and principles, while others apply the principles of RCM, looking for application of the principles to the 20% of the problems causing the highest downtime, quality cost, or maintenance cost.
All approaches use some common elements to arrive at the most value-added PM strategy for the equipment. When optimizing PMs, we will look at failure data, PMs, experience, and functional diagrams to develop a list of probable failure modes. We will then use the concepts of failure patterns, P to F curves, consequence, and operating context to develop an improved strategy.
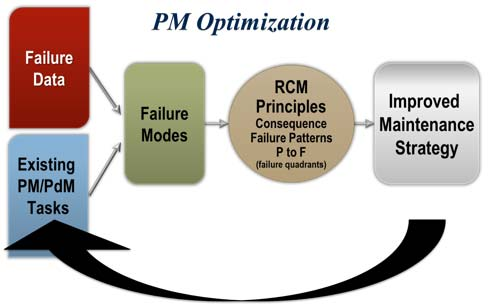
Using operating environment, failure patterns, and P to F, we can answer three basic questions
- Will replacement of part on a known interval or usage reduce the probability of failure?
- Can we see it in the process of failure with sufficient time to respond?
- Is the impact of the failure high enough to warrant the cost of a PM strategy?
These three elements will help us to determine the type of PM strategy that is value-added. In addition to developing the most value-added strategy, we can increase the standardization and quality of PM execution by developing steps and standards for PM tasks. We ask five simple questions when creating the PM task to improve the PM standard. We find that a high consequence, value-added PM should address the steps, criteria, references, and, of course, include safety information. To support this development we utilize the following five simple steps:
- What is to be done?
- How is it to be done?
- What is acceptable?
- Condition-based—what criteria or specification determines pass or fail?
- Interval-based—what criteria or equipment function must be ensured after task completion?
- What course of action should the craftsman take if the results are unacceptable?
- What do we do to ensure safety?
We will list the safety instructions first on the job plan, but we must understand what is to be done and how before we can determine the safety implications.
To summarize this information into a simple concept, it might be helpful to consider the following questions. While this might not be the most effective way to process many tasks, it does help us understand the process.
- What is the specific failure you are trying to stop (Failure Mode)?
- What is the history related to this failure?
- Is this the only task addressing this failure?
- Can you see the failure coming (P to F)?
- Can you predict when the failure is likely to occur (age)?
- How much impact would there be on Safety, Production, Cost…
- (Consequence) if this were to occur?
- Can you add more detail or pictures to the task to ensure higher quality of execution (What, how, criteria, what if fails)?
- How long would you feel comfortable letting this run without checking or changing (Frequency)?
- Who is the best resource to perform the task?