Building wiring is the electrical wiring and associated devices such as switches, meters and light fittings used in buildings or other structures. Electrical wiring uses insulated conductors.
Wires and cables are rated by the circuit voltage, temperature and environmental conditions (moisture, sunlight, oil, chemicals) in which they can be used, and their maximum current. Wiring safety codes vary by country, and the International Electrotechnical Commission (IEC) is attempting to standardise wiring amongst member countries. Colour codes are used to distinguish line, neutral and earth (ground) wires.
To enable wires to be easily and safely identified, all common wiring safety codes mandate a colour scheme for the insulation on power conductors. In a typical electrical code, some colour-coding is mandatory, while some may be optional. Many local rules and exceptions exist per country, state or region. Older installations vary in colour codes, and colours may fade with insulation exposure to heat, light and ageing. Color codes for India, are
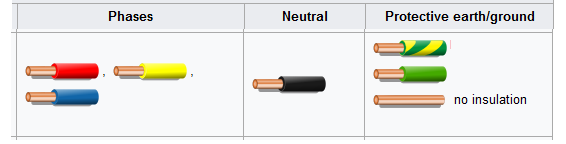
A power cable is an assembly of one or more electrical conductors, usually held together with an overall sheath. The assembly is used for transmission of electrical power. Power cables may be installed as permanent wiring within buildings, buried in the ground, run overhead, or exposed.
Cables consist of three major components: conductors, insulation, protective jacket. The makeup of individual cables varies according to application. The construction and material are determined by three main factors:
- Working voltage, determining the thickness of the insulation;
- Current-carrying capacity, determining the cross-sectional size of the conductor(s);
- Environmental conditions such as temperature, water, chemical or sunlight exposure, and mechanical impact, determining the form and composition of the outer cable jacket.
Copper conductor – Electrical devices often contain copper conductors because of their multiple beneficial properties, including their high electrical conductivity, tensile strength, ductility, creep resistance, corrosion resistance, thermal conductivity, coefficient of thermal expansion, solderability, resistance to electrical overloads, compatibility with electrical insulators and ease of installation.
Aluminium conductor – Terminal blocks for joining aluminium and copper conductors. The terminal blocks may be mounted on a DIN rail. Aluminium wire was common in residential wiring from the late 1960s to mid-1970s due to the rising cost of copper. Because of its greater resistivity, aluminium wiring requires larger conductors than copper. For instance, instead of 14 AWG (American wire gauge) copper wire, aluminium wiring would need to be 12 AWG on a typical 15 ampere lighting circuit, though local building codes vary.
PVC – Cables for industrial, commercial and apartment buildings may contain many insulated conductors in an overall jacket, with helical tape steel or aluminium armour, or steel wire armour, and perhaps as well an overall PVC or lead jacket for protection from moisture and physical damage. Cables intended for very flexible service or in marine applications may be protected by woven bronze wires. Power or communications cables (e.g., computer networking) that are routed in or through air-handling spaces (plenums) of office buildings are required under the model building code to be either encased in metal conduit, or rated for low flame and smoke production.
Usage – In construction of a house/ building house owner should focus on electric works also; which need a lot of attention while laying wiring as well as quality of wiring, specification of electric appliances and cables/wires. Due to carelessness or lack of knowledge by electrician fatal accidents may occur in later and take up more money in repair. Thus every care should be taken while doing electrical fittings. Here are given some tips on how to lay wiring.
Electrical cables/wires are laid inside walls and RCC slab which may require dismantling if any problem/defect arises in later. Dismantling is very costly as compared to getting it rightly fixed first time. In case of defects in electrical wires they can cause fire in house and may even take human life in some cases. So make sure you do the following to ensure good electric works.
- A professional or good electrician should be hired for electric works. All electric works and installations should comply with latest Indian Electricity Acts and Rules in all respects.
- All materials used in electrical fittings should be of approved and from a reputed manufacturer as per ISI specifications.
- Make sure that electrician has calculated total load from various items that would be used in the house. Whether he lays wires that are capable of taking total load.
- It is seen that a lot of times electricians are careless while putting right load bearing wires for a purpose and these wires get burnt at the movement when entire load is put on wires.
Electrical panels are easily accessible junction boxes used to reroute and switch electrical services. The term is often used to refer to circuit breaker panels or fuseboxes. Local codes can specify physical clearance around the panels.
Repairs – Any electrical repair project begins with safety. Before dismantling a lamp or appliance, unplug it. Shut off power to the circuit before working on a light fixture.
To diagnose a problem you often use a continuity tester, which we’ll explain in this section. It tells you whether there is a break (i.e., a lack of continuity) along the length of a wire, or whether the contacts of an electrical device have broken. It can help you isolate and identify the problem: a bad plug, cord, socket, or switch.
Lamps, which plug in, and light fixtures, which are permanently connected to household circuits, are wired in much the same way. Most parts, such as sockets and cords, are widely available at reasonable cost. Repair techniques are largely a matter of common sense: Pull the new cord through the lamp to replace the old cord, or replace a faulty socket with a new one of the same type. Wire new components the same way as the old ones.
Electrical work is safe if you always follow the most important safety measure: Shut off power and test to make sure power is off before you start the project. Review our safety tips before beginning any wiring project.
Earthing
Earthing means connecting any non-current carrying conductor part of an electrical system with general mass of earth in such a manner that there is an immediate discharge of electrical energy to the earth in the event of electrical potential developed at that part of the system. For example, metallic frame work of electrical appliances, metallic covering of electrical cables, the earth terminal of three pin socket outlets, stay wires and also neutral point of single phase and three phase supply systems must be properly earthed. Earthing is done to ensure that no current carrying part of the system rises to be potential beyond its normal value, no non-current carrying conducting part of a system rises to a potential beyond earth potential that is zero. Proper earthing also helps to avoid electrical shock to the human beings also to avoid the chance of fire hazard due to leakage current through unwanted path.
Properly designed, constructed and installed electrical equipments and appliances should not have any of the non-current carrying conducting parts which is in contact with any current carrying part. But accidentally may be due to failure of insulation between current carrying and non-current carrying conducting parts of the equipment/appliance, if any of the non-current carrying conducting parts comes in contact with any of the current carrying parts of the equipment/appliance, there will be a static electrical charge developed in the non-current carrying conducting part.
In the construction of most commercial buildings, one ground is usually run throughout the building to keep the impedance as low as possible. Low impedance in the ground is needed to make sure that the fuse blows when something gets short circuited to ground wire (for example cable insulation breaks inside the equipment and touches the grounded metal case). The grounding system is primarily designed for electrical safety in mind. The Protective Earth connection should be able to carry a heavy current to protect the user from live-to-chassis faults by ensuring that the fuse or circuit breaker will operate so the requirement is that the Protective Earth conductors can carry a 25A fault current for at least 1 minute. The grounding system in the building electricity distribution has only effect on the electromagnetic environment inside the building which you must understand.
Unfortunately all building have big electrical equipment such as air conditioning units, refrigerators, washers/dryers and other high current devices connected to the building ground (the same ground you use for your AV system). Computers and other equipments which use stitched power supplies generate harmonics to the electrical power which usually end up being noise in the grounding system. Light dimmers are also a strong source of interference and some of it typically ends to the ground wires also. Thus the chances of getting a clean ground in a typical audio visual installation is slim, especially in large commercial buildings, hotels, hospitals or convention centers.
Component parts of earthing system are to include the following:
- Earth electrode (rods, tapes etc.)
- Main earthing terminals or bars
- Earthing conductors
- Protective conductors
- Equipotential bonding conductors
- Electrically independent earth electrodes for special systems (clean earth)
- Accessories and termination fittings, bonding, welding kits and other materials