Drum Buffer Rope (DBR) is a planning and scheduling solution derived from the Theory of Constraints (ToC). The fundamental assumption of DBR is that within any plant there is one or a limited number of scarce resources which control the overall output of that plant. This is the “drum”, which sets the pace for all other resources.
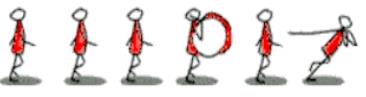
In order to maximize the output of the system, planning and execution behaviors are focused on exploiting the drum, protecting it against disruption through the use of “time buffers”, and synchronizing or subordinating all other resources and decisions to the activity of the drum through a mechanism that is akin to a “rope”.
The buffer is a period of time to protect the drum resource from problems that occur upstream from the drum operation. Its effect to provide a resynchronization of the work as it flows through the plant. The buffer compensates for process variation, and makes DBR schedules very stable, immune to most problems. It has the additional effect of eliminating the need for 100% accurate data for scheduling. It allows the user to produce a “good enough” schedule that will generate superior results over almost every other scheduling method.
Since the buffer aggregates variation, it also allows to operate the plant with much lower levels of work in process, producing dramatic reductions in production lead times and generating a lot of cash that was tied up on inventory. The “extra” capacity at the non-constraints helps, too. Since the plant is not overloaded with work it cannot do, the resources can “catch up” when problems strike, without affecting the drum or global throughput. After the drum has been scheduled, material release and shipping are connected to it, using the buffer offset. Material is released at the same rate as the drum can consume it. Orders are shipped at the rate of drum production.
DBR Scheduling Algorithm – The process of scheduling the factory first focuses on the primary objective of the facility, to ship to committed delivery date. Thus we first find the due date of the order, and add a shipping buffer to create an “ideal” finish date with confidence.
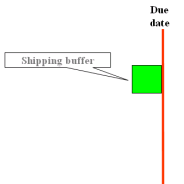
From this planned finish date, the order is backward scheduled to identify an “ideal” time to work on the drum resource, a “latest due by” (LBD) date.
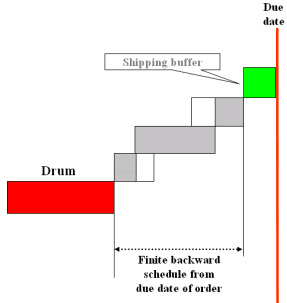
All orders are scheduled to fit on the drum using two passes; first, by assigning all batches an ideal placement on the drum schedule.
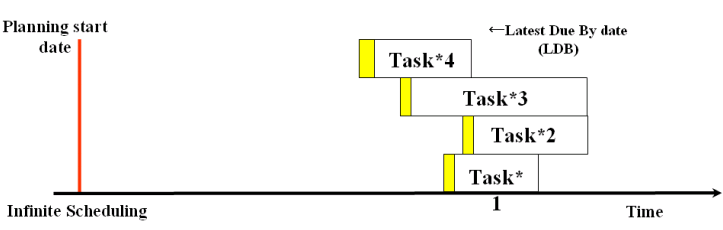
When the batch does not fit, i.e., there is another occupying its space, the batch is scheduled earlier in time so the order due date is not violated. This may result in some jobs starting before today, and not all jobs may be ready to start at the drum resource

The drum is then forward scheduled to resolve these conflicts, and potentially late jobs are identified (the Task 2).
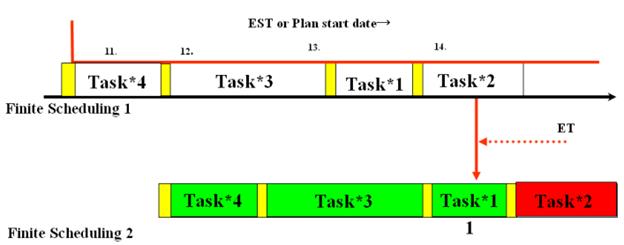
After the drum is schedule, the operations after the drum are scheduled forward in time from the drum completion date. Then, the jobs feeding the drum are backward scheduled from the start of the resource buffer.
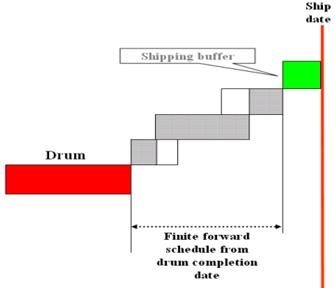