How do you sustain the newly achieved improvement? This phase is a mini version of process management. The team has been building and implementing the Six Sigma project , and during the Control Phase they begin to document exactly how they want to pass that structure on to the employees who work within the process. The phase will generate a detailed solution monitoring plan, observe implemented improvements for success, update plan records on a regular basis, and maintain a workable employee training routine.
A Control Plan is the key to sustaining the gains from a Six Sigma project. A Control Plan exists to ensure that we consistently operate our processes such that product always meets customer requirements as it ties together the elements of Six Sigma improvement activity. it allows Champions and other stakeholders to have confidence that the process improvements made will be robust. The Control Plan is a guide for the Process Owner to assist in tracking and correcting the performance of the KPIV’s and KPOV’s.
It is used to develop a detailed but simple document to clarify the details around controlling the key inputs and key outputs for which all the improvement efforts have implemented. Once the project is closed it is not necessarily over. The Control Plan is one part of ensuring the gains are maintained. If process performance strays out of control there are details and tools to adjust and re-monitor to ensure there has not been an over adjustment.
It is possible that the new performance capability warrants the calculation of new control limits. If so, the test(s) used, evidence, and new control limits should also be a part of this document. It is ideal to have a simple one-page document but if appendices and attachments are needed to ensure understanding and control then include this information.
It includes all relevant material and information it takes to ensure the gains are sustained and even further improved should be included. Often times there are long-term action items and the project list (possibly utilize a Gantt Chart) shall be updated and followed by the Process Owner until those actions are complete. The GB/BB will often move on to another project after the team disbands but follow up is often required weeks or months later. The follow up is done in conjunction with the Process Owner and possibly the Controller. Adhering to the details of the Control Plan will standardize these efforts and allow quick analysis of current performance.
A Control Plan provides a single point of reference for understanding process characteristics, specifications, and standard operation procedures also known as SOP for the process. A control plan enables assignment of responsibility for each activity within the process. This ensures that the process is executed smoothly and is sustainable in the long run.
A good Control Plan needs to be based on a well thought out strategy. A good control plan strategy should minimize the need of tampering the process. It should also clearly state the actions to be taken for out-of-control conditions. It should also raise appropriate indicators to indicate the need for Kaizen activities. A Control Strategy should describe the training requirements to ensure that everyone on the team is familiar with the standard operating procedures. In the case of an equipment control plan, it should also include details about maintenance schedule requirements.
The intent of an effective Control Plan Strategy is to
- Operate our processes consistently on target with minimum variation
- Minimize process tampering (over-adjustment)
- Assure that the process improvements that have been identified and implemented become institutionalized
- Provide for adequate training in all procedures
- Include required maintenance schedules
Control Plan inputs includes all processes, measurement systems and resources that need to be monitored and controlled
The elements of control plan includes process map steps, key process output variables, targets & specs, key and critical process input variables with appropriate working tolerances and control limits, important noise variables (uncontrollable inputs) and short and long term capability analysis results. Other element of control plan is designated control methods, tools and systems (spc, automated process control, checklists, mistake proofing systems and standard operating procedures),training materials, maintenance schedules and reaction plan and responsibilities
The plan should be developed by the project team in conjunction with those who will be responsible for the day to day running of the processes. The plan should be validated and then be subject to regular review, as part of the overall management system
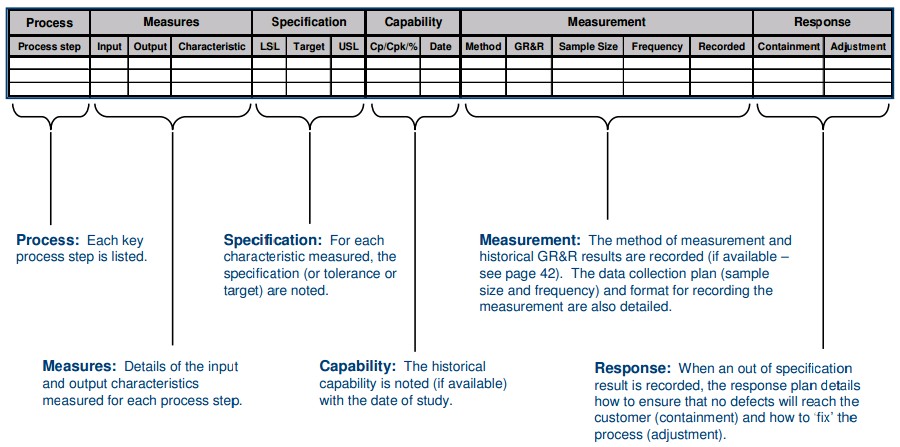
First of all, a control plan needs documentation that reflects the current methods of control and measurement systems. It is extremely important for the document to be current, since processes are continually being improved. The plan also needs to be developed around a single process or family of processes. Lastly, it needs to be updated by the process owner, since this will be the person or persons who has the most expertise in that process from end-to-end, and who would be most suited to making sure the processes are up-to-date and maintained.