While designing a control system, controllable and uncontrollable losses should be distinguished. The system should determine standard levels which can be attained. Losses may be uncontrollable in the short-term but controllable over a period of time. Moreover, it takes time to control a new process. The various levels should be frequently reviewed. Losses can be minimized by proper storage, proper handling, maintenance of suitable inventory levels etc.
A control system should calculate and report production and data regarding waste, scrap, spoilage and defectives should be regularly collected. Periodic reports help to evaluate performance and also in taking corrective action. Standards should be set. Variances of actual from standards should be examined so that it can be effectively controlled.
The control of losses can be exercised at three levels:
- Occurrence
- Recovery, handling and storage
Control over Occurrence
Losses are incurred due to nature of the product, quality control, method of production etc. The causes may be summarized as follows:
- Labour-related causes: Lack of training errors committed by machine operator, inadequate supervision, damage caused by handling carelessness, fatigue etc.
- Causes related to manufacturing method: Defective equipments, pitfall in design, machine jams, trials and adjustments, overloading and excessive utilization of resources, problems associated with new products, standards set etc.
- Materials related causes: Defective materials, obsolescence, evaporation, deterioratio
- Others: Strict inspection, thefts, etc.
Control Over Recovery Handling and Storage
As soon as stores are received they should be handled and stored properly. Different types of losses should be identified at different stages of production. Items to be rectified should be identified. Good handling and proper storage protect goods from damage, theft and misappropriation.
Control over Disposal
To maximize the sales value of waste, scrap, spoilage etc. the following points are to be considered:
- Make the goods ready for sale
- Select the best buyer
- Control the quantities of losses.
Bids may be obtained and prices obtained should be comparable with market prices. Physical control should be exercised over the quantities of scrap, spoilage leaving the factory and the quantities produced, repaired and sold must be continuously reviewed.
Illustration 3
2,000 kg. of Art Board valued at 8,000 were issued for the manufacture of medium sized cartons. The following details were collected:
- 2,400 Nos. medium sized cartons weighing 0.50 kg. each were manufactured.
- 480 kg. of off cuts were used for the manufacture of small sized carton. This would have amounted to 1,000.
- 320 medium sized cartons were damaged and rectification costs came up to 160.
- 120 kg. of off cuts were sold as scrap for 20.
You are required to calculate the cost of one medium sized carton assuming that there are no opening or closing stocks.
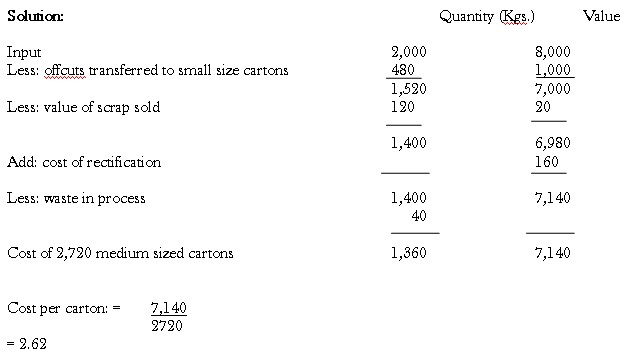
Notes:
- Calculation of waste in process each carton weighs 0.5 kg. Total medium sized cartons produced are 2,720. This means that quantity should be 2,720 x 1/2 = 1,360 Kgs. The balance quantity is presumed to be normal waste in process.
- The waste in one process may be used in another. The credit given to the process where loss occurs depends upon the utility value of this material for the process in which it is used, i.e., the value if it is directly purchased from the market.