This can, however, take the form of a random check of certain product lines rather than checking the whole consignment. A count of total pallets may be sufficient. Random checks are undertaken and any discrepancies found are charged to the supplier on a pro rata basis. This enables drivers to continue with their deliveries and pressurizes suppliers to increase the accuracy of their shipments. This can be extended to other operations, providing agreements can be made with the suppliers.
By measuring supplier performance a warehouse manager can also decide on the regularity and comprehensiveness of inbound product checks. The rate of checking can be based on the accuracy of recent deliveries. Initially the checks are 10 per cent of the lines on each incoming shipment. If they find a discrepancy they will check a further 10 per cent. Further discrepancies result in the whole load being checked. Where new suppliers are concerned it is likely that you will want to check the whole of the consignment initially until you are confident of the accuracy of the supplier.
There is a trade-off here between the time it takes to check inbound deliveries, the number of discrepancies found and the time it takes to deal with them. Another decision to be made is whether the delivery notes are used to check off the delivery or whether a ‘blind’ count is made (in which operators are not made aware of the quantities expected until the count has been completed) and the actual delivery cross checked against the paperwork once the whole load has been received into the warehouse. From experience, although it is likely to take longer, it is more accurate to count the product and then compare it with the delivery paperwork than use the paperwork as a checklist. The utilization of barcode scanners has speeded up the process significantly and improved accuracy.
Product can be scanned and the details compared in real time with the expected quantities to determine any discrepancies. Once scanned, the goods can be moved directly to the next staging point, be this quality control, a forward pick face, reserve storage or the dispatch bay for cross docking. The introduction of RFID will further reduce checking time at the receiving bay. Products that have tags fitted can be recognized and counted immediately on entry to the warehouse and details passed in real time to the WMS.
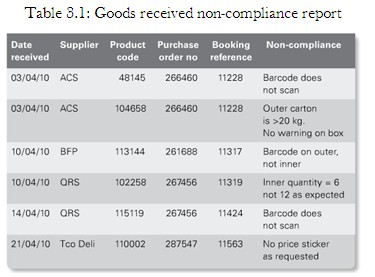