‘Supply Chain Management’ is defined as the integration-oriented skills required for providing competitive advantage to the organization that are basis for successful supply chains. A typical supply chain may involve a variety to stage. These supply chain stages include:
- Customers
- Retailers
- Wholesaler/ Distributors
- Manufacturers
- Component/Raw material suppliers
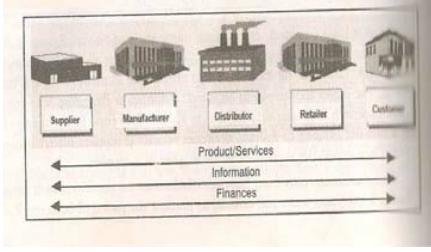
The concept of a supply chain is shown in Figure 9.1.8. Though many stages are shown in the figure, each stage need not be present in a supply chain. The number of stages included should meet that the organization generates profits for itself.
‘Supply Chain Management’ is the integration-oriented skills required for providing competitive advantage to the organization that are basis for successful supply chains.
‘Supply Chain Management’ can be defined as the active management of supply chain activities to maximize customer value and achieve a sustainable competitive advantage. It represents a conscious effort by the supply chain firms to develop and run supply chains in the most effective and efficient ways possible.
Within each organization, such as a manufacturer, the supply chain includes all functions involved in receiving in receiving and filling a customer request. The functions that are chain includes all functions involved in receiving and filling a customer request, operations, distribution, finance, and customer service. The decision is tradeoff between price, inventory, and responsiveness.
Its activities begin with a customer order and ends when a satisfied customer has paid for his or her purchase. Generally, more than one player is involved at each stage. A manufacturer may receive materials from several suppliers and then supply several distributors. Thus, most supply chains are actually networks.
Supply chain is an integral part of the value chain. According to Michael Porter, who first articulated the value chain concept in the 1980s, the value chain is comprised of both the primary and support activities. The supply chain, consists only of the primary activities or the operational part of the value chain. The supply chain, therefore, can be thought of as a subset of the value chain. In other words, while everyone in the same organization works in the value chain, not everyone within the organization works in the supply chain.
The value a supply chain generates is the difference between what the final product is worth to the customer and the effort the supply chain expends in filling the customer’s request. The supply chain profitability is based on the effort involved in the appropriate management of the flows between and among stages in a supply chain. Unlike the traditional measure of organizational success in terms of the profits at an individual stage, supply chain success is measured in terms of supply chain profitability.
The objective of every supply chain is to maximize the overall value generated so that the final price of the good covers all of the costs involved plus a profit for each participant in the chain. Figure 9.1.8.2 shows the supply chain as a network and also as a part of the value chain.
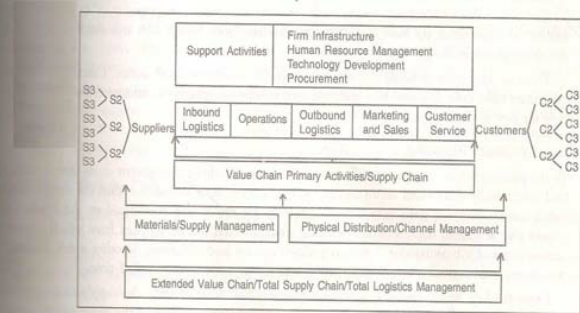
The appropriate design of the supply chain will depend on both the customer’s needs and the role of the stages involved. In some cases, a manufacturer may fill customer orders directly. For example, Dell has been one of the most successful examples of effective supply chain management. Dell builds-to-order, that is, a customer order initiates manufacturing at Dell. Dell does not have a retailer, wholesaler, or distributor in its supply chain. While other computer companies must stock a month of inventory. Dell carries only a few days worth. In fact, many of the components are delivered within hours of being assembled and shipped to the customer. It plans orders and signals suppliers every two hours, which enables it to manufacture and deliver exactly what its customers want.
In other cases, such as in a mail order business like Amazon.com, the company maintains an inventory of product from which they fill customer orders. In the case of retail stores, the supply chain may also contain a wholesaler or distributor between the store and the manufacturer.
Decisions in a Supply Chain
Supply chain management involves proactively managing the two-way movement and coordination (that is, the flows) of goods, services, information, and funds from raw material through end user. A company with a “supply chain orientation” is one that recognizes the strategic value of managing operational activities and flows across a supply chain. It s decision fall into three categories of phases:
Supply Chain Design
Supply Chain Design is a strategic decision. If reflects the structure of the supply chain over the next several years. It decides what the chain’s configuration will be, how resources will be allocated, and what processes each stage will perform.
Successful design requires a high degree of functional and organizational integration. In order to do so, it is essential to develop supply chain process maps (flow charts) for major supply chains and their related processes helps establish an understanding of the supply chain. There should be a clearly understood mapping convention to be utilized, along with other information requirements. The objective of this exercise is to develop supply chain maps that present all supply chain entities along with key processes.
From this exercise will flow such decisions as the location and capacities of production and warehousing facilities, the products to be manufactured or stored at various locations, the modes of transportation, and the type of information system to be utilized. The organization must also identify key and critical supply chains components. It must be knowledgeable regarding its part of the supply chain and also must understand how the part interfaces with the other parts of the supply chain.
The supply chain configuration should support the organization’s strategic objectives. In the case of TI Cycles regarding the location and capacity of its manufacturing facilities at Aurangabad, the joint manufacturing agreement with Avon Cycle and distribution network are all supply chain design or strategic decisions.
These are long-term decision and are very expensive to alter on short notice. Consequently, when companies make these decisions, they must take into account uncertainty in anticipated market conditions over the next few years.
Supply Chain Planning
In the planning phase, companies define a set of operating policies that govern short-term operations and are normally determined on an annual basis. These decisions are made within the supply chain’s configuration. Planning starts with a demand forecast for the coming year. Based on the demand, an annual plan is worked out. Decisions regarding which markets will be supplied from which locations, outsourcing and sub- contracting, inventory policies, etc. are made. Planning, in other words, establishes parameters within which a supply chain will function over a specified period of time.
One the key supply chains have been identified, one must identify the supply chain member organizations (suppliers and customers) that are considered most critical to the organization’s supply chain management efforts. In selecting external members, several issues should be addressed.
- SCM endeavors are likely to be more productive if participating organization are not direct competitors. There may be limits to collaborative supply chain efforts when both buyer-supplier and competitor relationships exist between participating organizations.
- All organizations and their representatives must be pursuing similar goals. This does not mean that each organization should have identical goals, but that their respective goals must be compatible with the overall SCM initiative.
- SCM initiative is unlikely to be successful unless all members from each organization involved feel they are benefiting from participation. SCM efforts have to be focused where the involvement is beneficial to all the members.
In well managed organizations, in the planning phase uncertainty in demand, exchange rates, and competition over this time horizon are included in the decisions. Given a shorter time horizon and better forecasts than the design phase, the planning phase tries to exploit the supply chain design to optimize performance.
Supply Chain Operation
This has a short-term time horizon, monthly, weekly or daily. The focus, during this phase, it on individual customer orders at the operational level, within planning policies, the goal is to handle incoming customer orders in the best possible manner. Firms allocate inventory or production to individual orders, set a date that an order is to be filled, generate pick lists at a warehouse, allocate an order to a particular shipping mode and shipment, set delivery schedules of trucks, and place replenishment orders.
Aggregate planning is the basis for decisions at this stage. The aggregate plan serves as a broad blueprint for operations and establishes the parameters within which short-term production and distribution decisions are made. It allows the supply chain to alter capacity allocations and change supply contracts. In addition, man constraints that must be considered in aggregate planning come from supply chain partners outside the enterprise, particularly upstream supply chain partners. Without these inputs from both up and down the supply chain, aggregate planning cannot realize its full potential to create value.
The output from aggregate planning is also of value to both upstream and downstream partners. Production plans for an organization define demand from suppliers and establish supply constraint for customers. If a manufacturer has planned an increase in production over a given time period, the supplier, the transporter, and warehousing partner must be aware of this plan and incorporate the increase in their own plans.
Because operation decisions are being made in the short term, there is less uncertainty about demand information. Given the constraints established by the configuration and planning policies, the goal during the operation phase is to exploit the reduction of uncertainty and optimize performance.
Ideally, all stages of the supply chain should work together to optimize supply chain performance. An important supply chain issue is collaboration with downstream supply chain. Therefore, it is important to perform aggregate plans over as wide a scope of the supply chain as is reasonably possible.
Introduction to ERP
In the early 1990s many large companies realized that it was time to update their existing information systems to take advantage of new technologies. Programs written in programming languages such as COBOL, PLI, RPG, and assembler were becoming increasingly expensive to maintain. Further the mainframe computer technology was not cost defective compared to the ever more powerful and inexpensive microprocessor- based computer. Change was inevitable. And SAP offered a comprehensive solution. SAPAG, a German firm, is the world leader in providing ERP software. Its flagship product is known as R/3.
The software is designed to operate in a three-tier client / server configuration. The core of the system is a high-speed network of database servers. These database servers are special computers designed to efficiently handle a large database of information.
The R/3 applications are fully integrated so that data are shared between all applications. If for example an employee posts a shipping transaction in the sales and Distribution module, the transaction is immediately seen by Accounts payable in the Financial Accounting module, and by inventory management in the materials management module. Much of the success of the product is due to the comprehensive coverage of business applications. In a sense, SAP has changed the face of information technology.
R/3 Application Modules
R/3 is built around a comprehensive set of application modules that can be used either alone or in combination. The modules the makeup R/3 the emphasis is placed on what these modules actually does, not on the technical aspects of how they communicate with one another.
SAP organizes the R/3 modules in a variety of ways in its documents. In general, there are four major elements to the organization: financial accounting, human resources, manufacturing and logistics, and sales and distribution.
Financial Accounting
The financial accounting segment of R/3 includes three major categories of functionality needed to run the financial accounts for a company financials (FI), controlling (co), and asset management (AM)
As with all the modules in the R/3 system, the user will find all information current and integrated. Thus an individual manufacturing plant or sales organization can run a profit and loss report at any time during the month and be shown the most up to date information.
The controlling category includes costing; cost center, profit center, and enterprise accounting and planning; internal order; open item management; posting and allocating; profitability analysis; and a variety of reporting functions. It also includes a project system to track activity and costs related to major corporate projects, such as the implement of an R/3 system.
Also include is a module of all activity based costing (ABC) to other types of costing approaches.
The asset management category includes the ability to manage all types of corporate assets, including fixed assets, leased assed, and real estate. It also includes the capital investment management module, which provides the ability to manage, measure, and oversee capital investment programs.
Human Resource (HR)
The human resource (HR) segment contains the full set of capabilities needed to manage, schedule, pay, and hire the people who make a company run. It includes payroll, benefits administration, applicant data administration, personnel development planning, workforce planning schedule and shift planning, time management, and travel expenses accounting. Because the structure of most companies shifts frequently, one function in the human resource category provides the ability to represent organizational, charts, including organizational units, jobs, positions, workplaces, and tasks.
Capturing data from the human resources module, the SAP business workflow system allows management to define and manage the flow of work required in cross functional business process.
Manufacturing and Logistics
The manufacturing and logistics segment is the largest and most complex of the module categories. It can be divided into five major components:
- Material Management (MM),
- Process Maintenance (PM),
- Quality Management (QM),
- Production Planning and Control (PP) and
- Project Management System (PS)
Each component is divided into a number of subcomponents.
Plant maintenance supports the activities associated with planning and performing repairs and preventive maintenances. The quality management capability plans and implements procedures for inspection and quality assurance It is built on the ISO 9001 standard for quality management.
Production planning and control supports both discrete and process manufacturing process.
The project management system lets the user set up, manage, and evaluate large, complex, projects, whereas the financial costing project system focuses on costs, the manufacturing project system is used for planning and monitoring dates and resources. The system walks the user through the typical project steps: concept, rough cut planning, details planning approval, execution and closing it manages a sequence of activities each with its interrelationships to the others.
Sales and Distribution (SD)
The sales and distribution (SD) set of modules provides customer management; sales order management; configuration management; distribution export controls, shipping and transportation management; and billing, invoicing, and rebate processing.
In sales and distribution, produces or services are sold to customers. In implementing and SD module (as in other modules), the company structure must be represented in the system so that for example, R/3 known where and when to recognize revenue.
When a sales order is entered it automatically includes the correct information on pricing, promotions, and availability and shipping options. Batch order processing is available for specialized industries such as food, pharmaceutical, or chemical.
Lean Manufacturing
Lean manufacturing has emerged as an alternative to mass production techniques. It reflects a totally new approach to operation management and greatly contributes to the addressing of issues in a consumer driven market. In 1990, James Womack wrote a book called “The Machine that Changed the World”. This book was a straight forward account of the history of automobile manufacturing combined with the study of Japanese, American and European automobile assembly plants. He called the system that he described “Lean Manufacturing” It is an incredibly successful System that integrates the ‘routine’ work of producing and delivering products, services and information with ‘problem identification and process improvement’. It is an extension of supply chain concept based on a systematic elimination of unproductive activities identified as wastes.
The concept involved in minimizing wastes; all manufacturing processes are either value- added or non value- added. The valor stream includes all activities required to bring a product from vendor’s raw material into the hands of customers. Value –added processes mold, transforms or otherwise change raw material into finished products. Non value –added activities are often necessary, consume time and resources but add little or no value to the product. Such activities include transporting, material, storing material, conducting inspection etc.
To provide what the customer is asking for, you need to improve production efficiency. In the past, increasing production efficiency required employees to work harder or longer and machines to run faster. Such methods work in the short run but cause problems. Accident rates increase workers and equipment is overworked and overtaxed equipment and workers revolt.
The Lean concept refers to a collection of tools used to promote long-term profitability and growth by more with less.
The essential element of Lean Manufacturing is aimed at the elimination of waste at every area of production including customer relations, product design, and supplier network and factory management. Its’ goal is to incorporate less human effort , less inventory, less time to develop products and less space , to become highly responsive to customer demand, while producing top quality products in most efficient and economical manner possible. Total Productive Maintenance (TPM) is a Lean concept based on three simple ideas;
- Preventive maintenance schedules must be developed and adhered to,
- Extensive maintenance history exists in a database and equipment failures may be predicted within reasonable time frames
- Simpler maintenance tasks be delegated to those who know the equipment the best.
Establishing a preventive maintenance schedule and Predictive Maintenance Systems are basic requirements of Lean Manufacturing. In addition, the operators should be responsible and have ownership for all maintenance of the equipment they operate. As operators know their machines the best they would be the first to detect variations in operations; unusual sounds, vibrations smell etc. The specific tools of Lean Manufacturing such as
- Pull System,
- Kanban Cards,
- Kaizen
Are artifacts of a general? Comprehensive approach to managing collaborative work systems that allows frequent fine grained problem identification and improvement in overall organizational structure, coordinated mechanisms and task performance.